2020年是極不平凡的一年,新冠疫情肆虐全球,導致工業生產、科技發展均經受了前所未有的挑戰,全球經濟增長明顯放緩。雖然如此,軍工材料技術依然保持快速發展的態勢,為武器裝備的發展提供源源不斷的創新動力。過去兩年,我們連續推出了“國外軍工材料技術重大發展動向”,通過回顧年度軍工材料領域的十個重大事件,觀察行業發展動向,研判未來軍工材料的發展趨勢,啟發廣大讀者和科研工作者,提供探討平臺。兩年以來,這項工作取得了不錯的反響。
2020年,復合材料、金屬等結構材料及防彈、密封等功能材料在裝備應用及前沿探索兩個層面均有上乘表現;電子信息功能材料和制造技術不斷發展;計算材料學和人工智能技術形成合力,使高熵合金、新型超硬合金等新材料發現進程加快。2021年1月19日,中國航空工業發展研究中心在北京組織專家開展了“2020年度國外軍工材料重大動向”評選工作,本著重大性、先進性、引領性、基礎性四大原則,從高性能金屬材料、先進復合材料、特種功能材料、電子信息功能材料、關鍵原材料等五大領域共計80條發展動向中,遴選出以下10條重大技術動向,供決策機構、科研單位和廣大讀者參考。
一、3D打印技術成為復合材料低成本化的重要途徑
纖維增強樹脂基復合材料性能優異,但制造工藝繁雜且成本高昂。3D打印可以減少人力和加工成本,以更節能、更快速、更可靠的方式制造復合材料,同時減少結構缺陷。此外,3D打印不再需要特殊工具或模具,能夠直接制造任何形狀的纖維增強復合材料,因此可取代更復雜、耗時且昂貴的傳統制造技術。隨著技術的不斷成熟,3D打印技術正推動實現復合材料的性能和成本的最優組合。
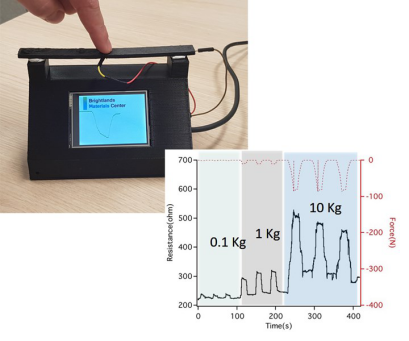
圖1 荷蘭Brightlands材料中心開發了具有自感知功能的3D打印復合材料試驗件(圖片來源:Brightlands)
3D打印技術推動實現了結構功能一體化復合材料的制造。2020年4月,荷蘭Brightlands材料中心利用3D打印技術開發出一種碳纖維增強復合材料零件,利用結構形變產生測量電阻變化這一特性實現了材料的“自感知”功能,這為實現飛機結構健康監測(SHM)能力創造了條件。3D打印技術可以非常精確地定位和定向連續碳纖維,因此,將纖維嵌入產品結構內部的選定方向和位置,使其在沿特定載荷路徑提供所需強度和剛度的同時,還可發揮結構監測“傳感器”的作用,多條纖維可在整個零部件中形成一系列不同類型的傳感器。這些纖維“傳感器”在測試過程中監控和收集結構載荷變化情況,將信息實時反饋,便于3D打印結構設計的優化。研究成果對于飛機結構健康監測意義重大,同時還有望進一步實現飛機結構重量的降低和飛行效率的提升。
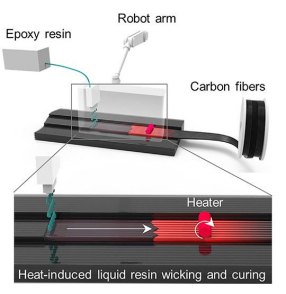
圖2 特拉華大學研究人員設計的新型3D打印方法示意圖。其中加熱裝置接觸并沿著碳纖維移動,產生動態溫度梯度,觸發分配液體聚合物在碳纖維結構中注入并固化。(圖片來源:特拉華大學)
連續碳纖維3D打印技術取得突破。熱塑性復合材料和不連續短切纖維復合材料近年來已成功地實現3D打印,但受限于結構組成,得到的3D打印復合材料通常力學性能較差、使用溫度較低。3D打印連續碳纖維與熱固性聚合物構成的復合材料,能夠提供更加優異的力學性能和熱穩定性,過去受限于技術一直未能實現。2020年9月,美國特拉華大學開發了全新的局部平面熱輔助3D打印技術,首次實現了連續碳纖維3D打印,可與熱固性聚合物結合低成本、靈活地制造復合材料。局部平面熱輔助3D打印技術通過精確掌握碳纖維溫度,控制固化成所需形狀液態聚合物的厚度和固化程度,無需后固化。與需要數十小時后固化的傳統復合材料工藝相比,節省大量時間、成本和能耗。除此之外,研究團隊還開發了機器人系統,包括獨特接頭和自動機械臂,可滿足不同形狀結構的制造需求。局部平面熱輔助3D打印可以為許多行業提供快速、節能的制造方法。
二、多材料增材制造技術將推動金屬多功能化發展
增材制造技術已在金屬領域產生多項實際用例,并證明其顯著優勢。例如GE公司為LEAP系列航空發動機打造的燃油噴嘴,將原本需要20個金屬零件組裝而成的組件集成為一個增材制造部件,不僅減輕了25%的結構重量,還實現了耐用性的提升。傳統的增材制造技術包含多種工藝,如粉末床熔融、定向能量沉積、冷噴涂等。但不同的工藝受限于原材料和設備等因素:如必須使用某種特定材料才能實現,且得到的零部件的尺寸和外形也受到限制,制造成本往往高居不下。
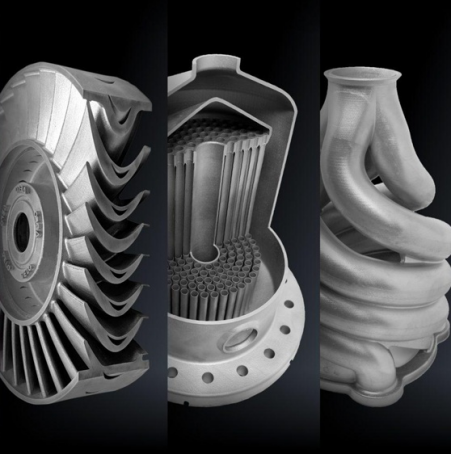
圖3 MULTI-FUN項目將聚焦新材料和新設備的開發,帶來具有多功能性的設計
2020年7月,為推進多材料、多工藝金屬增材制造的融合發展,來自8個歐洲國家的21個工業制造和科學研究領域機構聯合啟動了一項名為MULTI-FUN的項目。該項目為期3年,由歐盟地平線2020創新計劃資助,重點實現金屬增材制造領域2個重要戰略目標:一是通過使用集成多種功能特性的新型活性材料,顯著提高金屬增材制造產品的制造效率和綜合性能;二是通過開發和使用具有創新性、高效性、經濟性的增材制造技術,實現多材料、大尺寸、復雜結構的協同制造。該項目設置了四個具體目標:
目標一:開發5種專門用于增材制造的新材料,其中3種將使用納米技術。這些材料應具有顯著的熱、電和耐磨性能。該工作將帶來優質的金屬結構材料(鋁合金、低合金鋼等)與相應活性材料結合的解決方案,結合納米技術使所得新產品的效率、質量和可靠性提高至少40%,實現金屬的多功能化。
目標二:開發一套增材制造設備與增材制造軟件。利用目標一中開發的5種新材料,通過5項新技術,創造至少10種新的多材料組合。再通過軟硬件結合的方式,利用集成多種增材制造技術的設備,制造出至少7種面向不同應用場景的演示驗證零件。該工作的核心成果是創造出集成多種增材制造技術且能夠并行工作的設備。
目標三:制造和評估7個具有多材料設計且集成多種功能的演示驗證零件。7種零件涵蓋結構零件、模具和測試設備,涉及汽車、航空、航天和其他制造生產行業等4大領域。核心成果是利用基于多材料集成多功能,創造出提高質量和效率的新零件和新技術。
目標四:評估全壽命周期,降低增材制造技術的成本和環境影響。通過對增材制造過程中涉及的材料、硬件設備、工藝策略、零件設計和制造等所有環節的評估,改進對原材料和資源的利用,減少對環境的影響,并將成本降低35%。該工作將加深對增材制造技術的研究和認識,輔助制訂適用于多材料增材制造的行業標準并推動建立監管機構。
三、新型超輕不銹鋼較傳統不銹鋼減重約20%
鋼是全球工業化進程中的核心材料,其年產量超過18億噸。但鋼制結構的腐蝕造成的直接經濟損失超過2.5萬億美元。為了滿足以化工為代表的重點行業對于材料機械性能和良好耐腐蝕性能的要求,不銹鋼取得了良好的發展。基于鐵-鉻、鐵-鉻-碳和鐵-鉻-鎳體系開發的傳統不銹鋼,至少含有10.5%質量分數的鉻,盡管發展取得了巨大成功,但也迫使不銹鋼重量不斷增加。同時,由于鉻和鎳等關鍵元素較為昂貴,還帶來了巨大的環境和成本負擔。因此發展輕量化的不銹鋼對于可持續發展具有重要意義。傳統的超輕鋼材一般是在鋼中添加輕合金元素鋁實現的,但過量的鋁會導致脆性問題,因此鋁含量通常不能超過10%。
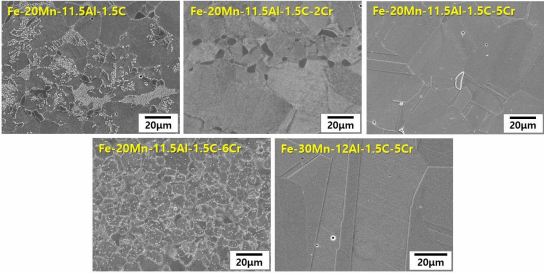
圖 4 基于Fe–(20–30)Mn–(11.5–12.0)Al–1.5C合金微觀組織隨著Cr含量的增加而變化。(圖片來源:《科技報告》)
為了解決這一問題,2020年11月,在韓國國防事業廳軍民合作振興院軍民兩用技術開發項目的支持下,韓國科技信息通信部下屬的韓國材料研究所與浦項產業科學研究院合作,對鋼種的碳、錳、鉻等元素的添加量進行了優化,在添加超過11.5%的鋁同時提升鋼的韌性,將傳統不銹鋼7.9-8.0克/立方厘米的密度降低至6.3-6.5克/立方厘米,得到了減重超過17%的超輕質不銹鋼,同時還兼具超高強度(>1GPa)和高延展性(>35%)。由于沒有添加昂貴的鎳,超輕質不銹鋼確保了價格競爭力。此外,通過添加鉻,鋼表面形成了鋁和鉻含量較高的致密氧化層,確保其耐腐蝕性與400系不銹鋼相當。這項研究從全新的合金設計角度出發,既突破了傳統不銹鋼的重量限制,同時也解決了超輕質鋼材的易腐蝕和脆性問題,意義重大。新型超輕質不銹鋼將優先應用于汽車、造船等行業,有望進一步提高燃油效率,降低二氧化碳排放。
四、新型核燃料向低鈾化轉變
高純度貧鈾是美國正在進行的國家核武器儲備現代化的重要戰略物資。然而,根據美國能源部國家核安全局的估計,貧鈾原料供應非常有限,其目前的貧鈾金屬供應將在本世紀20年代末耗盡。美國國家核安全局也不具備將貧鈾轉化制造成武器部件所需的全部能力,而這些部件是核儲備現代化所必需的。為減少對鈾的依賴,尋找能夠替代鈾的材料,開發新型核燃料迫在眉睫。
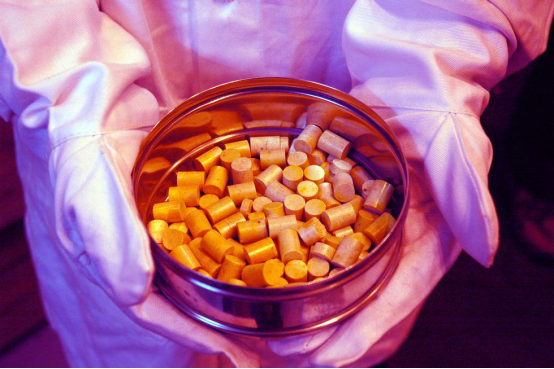
圖 5 顆粒形式的釷,這種放射性金屬材料保持強勁增長勢頭,將替代部分鈾成為新型核燃料中的重要組成部分。(圖片來源:Popular Mechanics)
2020年9月,美國能源部愛達荷國家實驗室、德克薩斯州農工大學核工程與科學中心、清潔堆芯釷基核能公司三方合作研發了一種名為ANEEL的新型核燃料。這種燃料是由放射性金屬釷和“高豐度低濃鈾”(鈾-235豐度在5%至20%范圍內)組成的混合物,將在美國生產,計劃出口至印度等新興核電市場,最快可以在2024年投入商業使用。金屬釷有較高的熔點和較低的工作溫度,抗堆芯熔毀能力強于金屬鈾。這種新型核燃料燃耗很深,可在反應堆中停留的時間更長,燃料利用率更高。此外,相較傳統的核燃料,新型核燃料使用了更少的鈾,產生廢物減少80%以上,“燃燒”時產生的钚也將進一步減少,有利于降低核燃料成本、防止核擴散、減少核廢物處理。
五、超高溫陶瓷打破4000℃耐溫大關
高超聲速飛行器機翼設計中將前緣的倒圓半徑減小到幾厘米,從而帶來升力和可操縱性顯著提升,同時減少空氣動力阻力。但是,當飛行器往返大氣層時,機翼蒙皮表面溫度可達2000°С,其最外側邊緣部位甚至將達到4000°С以上。因此,開發耐高溫材料和結構是當前高超聲速飛行的發展重點,也是設計過程中面臨的主要難點。
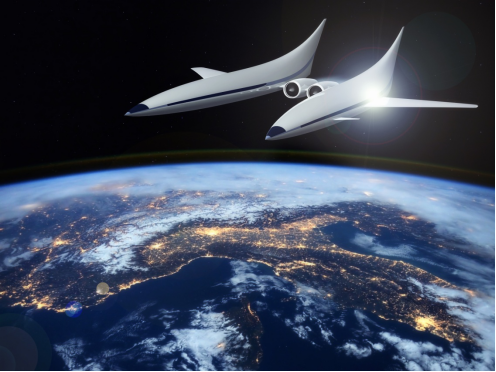
圖 6 基于鉿-碳-氮體系的新型高溫陶瓷材料有望成為解決高超聲速飛行器耐高溫結構的鑰匙(圖片來源:俄羅斯國立科技大學)
美國布朗大學曾預測,基于鉿-碳-氮(Hf-C-N)體系的陶瓷材料理論上具有目前所有材料中最高的熔點,理論值為4200℃左右,具有杰出的導熱性和抗氧化性。在此基礎上,2020年5月,俄羅斯國立科技大學的科研人員使用自蔓延高溫合成法,開發出基于鉿-碳-氮體系的新型高溫陶瓷材料,其化學式為HfC0.5N0.35。該材料不僅具有超過4000℃的熔點,其硬度達到21.3吉帕,高過目前最具應用前景的ZrB2/SiC(20.9吉帕)和HfB2/SiC/TaSi2(18.1吉帕)。新型陶瓷材料有望在飛機耐高溫部件,如噴氣發動機熱端部件和高超聲速飛機機翼前緣等部位應用,此外也可推廣應用至其他航空航天裝備、火箭導彈制造、特種軍事技術設備等領域。
六、輕量化成為防彈材料的發展重點
典型的防彈衣主要由芳綸“凱夫拉”纖維、超高分子聚乙烯纖維制成,但為了提升防彈性能而不斷增加的厚度和重量,造成防彈衣穿著舒適性降低,穿著者的機動靈活性和工作便捷性也受到較大影響。此外,直升機、運輸機等航空裝備對于防彈性能的要求越來越高,但受限于發動機性能,難以承受防彈結構無限的加厚加重。防彈材料高性能化、輕薄化,已成為該領域迫切需求和主流發展趨勢。
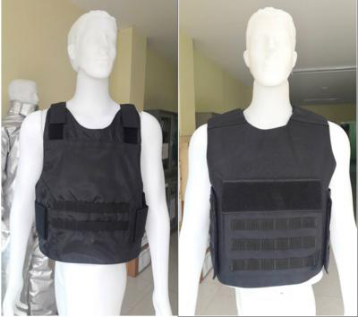
圖 7 2AM系列的石墨烯增強防彈背心(圖片來源:PlanarTech)
英國和泰國合作推廣使用了輕量化的石墨烯增強防彈衣。2020年4月,英國PlanarTech公司宣布與泰國IDEATI達成協議,推廣應用其2AM系列石墨烯增強防彈背心和防彈板產品。2AM是一種由石墨烯和超高分子聚乙烯組成的復合材料,它利用了石墨烯可顯著提升強度的特性來制造超輕型防彈衣。由2AM材料制成的A-10418產品,是目前市面上最薄(20毫米)、最輕(1.8千克)、且獲得美國國家司法協會(NIJ)彈測認證合格的IV級獨立防彈板。向復合材料中添加石墨烯納米顆粒可有效的將獨立防彈板背面變形程度(BFD)降低至僅11.3毫米。2AM系列產品已批量生產,并至少交付1000件供泰國皇家陸軍使用。未來也有望在防爆盾、防彈艙門等產品中取得應用。
圖 8 英國馬歇爾公司與奎奈蒂克公司合作的LAST Armor LWA裝甲材料(圖片來源:英國馬歇爾公司)
英國馬歇爾與奎奈蒂克合作推出新一代軍用裝甲材料。2020年8月,英國馬歇爾航空航天與防務集團與英國奎奈蒂克(QinetiQ)公司簽訂了獨家合作協議,銷售和安裝C-130“大力神”最新一代機型的輕型裝甲——LAST Armor LWA。這種裝甲由高強度聚乙烯制成,比目前在C-130J上應用的LAST裝甲解決方案輕約380千克,僅為舊款LAST裝甲重量的一半,能夠為機組人員提供同等的防護性能。在裝甲表面涂覆環保涂層后,即使在最惡劣的環境下,裝甲也可以保持化學惰性不腐蝕。由于結構輕質,可顯著節省飛機燃料,減少了對飛機重心的影響,使C-130-30變體機型具有完整的載荷能力。同時,在定期維護或者作為獨立部件使用時,裝甲可快速輕便的安裝和拆卸,確保以最佳狀態完成飛行任務。
七、新一代飛機超高溫防火密封件可在315℃下工作
專用防火密封件主要應用于飛機機身、吊架、反推力裝置和發動機等部件中,其主要作用是防止在正常工作條件下氣流從機體內特定的工作區域擴散至其他區域。對于飛機來說更加重要的一點是,使用專用防火密封件可預防由機內局部失火引發的更大事故,它可抑制火勢向機體其他部位蔓延,保證飛機在起火后仍擁有至少15分鐘的緩沖時間安全著陸,確保人身安全。因此,專用防火密封件耐熱溫度越高,可承受發動機內的極端環境溫度越高,理論上意味著飛機發動機性能越強,飛機的安全系數越好。
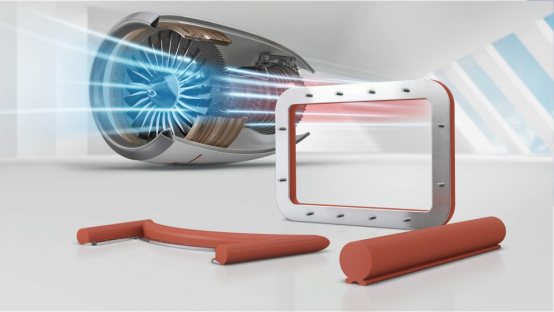
圖 9 瑞典制造商特瑞堡密封系統公司推出的新型超高溫密封件(圖片來源:特瑞堡)
2020年5月,瑞典制造商特瑞堡密封系統公司推出了一款超高溫密封件,可在-40℃到+315℃或更高的溫度下工作,遠超過其上一代產品。新一代超高溫密封件的全壽命周期為60000個飛行周期,克服了高溫下聚硅氧烷易松弛、易壓縮形變的固有特性,可在更高溫度的飛機發動機部位中使用。在熱浸試驗中,新一代超高溫密封件的性能優于其他防火密封件。在所有測試條件下,其性能損失均比要求的標準值至少低15%。特瑞堡利用專有技術,使新型密封件能夠適應任何幾何形狀,同時進一步減輕了結構重量并有效減少了零件數量,簡化了裝配過程,可直接對目前正在使用過程中的密封件產品進行替換。這款防火密封件的問世意味著飛機制造商可開發出性能更強、燃油效率更好的航空發動機,更好的落實可持續發展。
八、臺積電和三星在硅半導體3納米工藝上同臺競技
摩爾定律是對半導體行業發展規律的總結,在過去的數十年里一直對該行業的發展起到指引和推動作用。但隨著器件性能的提升、尺寸的縮小,晶體管特征尺寸已經達到原子級別,晶體管中的載流子將不受控制,短溝道效應、熱電子效應、漏電流增大等問題越來越嚴重。技術難度的增加和成本的急劇增長,使得先進工藝制程的研發速度逐漸放緩。目前14納米及以下的工藝大多采用立體結構,即鰭式場效晶體管(FinFET)。但這種結構的前道工藝已接近物理極限,如繼續微縮,電性能的提升和晶體管結構上都將遇到諸多問題。
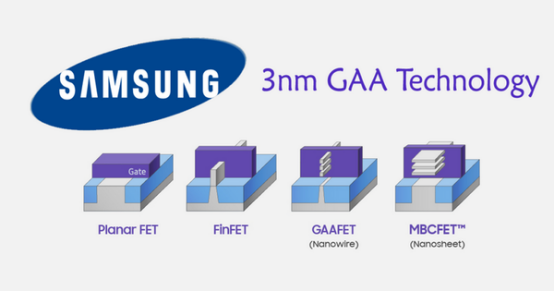
圖 10 三星在3納米芯片量產工藝中率先使用全環繞柵極晶體管架構(圖片來源:Ezone)
2020年1月,三星電子宣布計劃在全球范圍內率先實現3納米芯片量產制程工藝,以確保其在半導體市場的技術優勢。三星計劃較為激進放棄FinFET晶體管技術,率先采用基于全環繞柵極(GAA)晶體管架構的3納米技術。同5納米制程工藝相比,該技術能使芯片的理論面積縮小35%、能耗降低50%、性能提高30%。三星自2002年起一直在開發閘極全環工藝技術,通過使用納米片設備制造出了多橋-通道場效應管,確保減少功率泄漏,改善對通道的控制,這是縮小工藝制程的基本步驟。這種設計可實現更高效的晶體管設計,并具有更小的整體制程尺寸,從而在5納米FinFET工藝上實現了每瓦性能的巨大提升。新工藝的實現還需要對顯影、蒸鍍、蝕刻等一系列工程技術進行革新,且為減少寄生電容還需導入替代銅的鈷、釕等新材料。首批面向智能手機和其他移動終端的3納米芯片將于2020年進行測試,并于2021年批量生產。對高性能芯片改進型產品,如圖形處理器和封裝到數據中心的人工智能芯片,將在2022年實現批量生產。
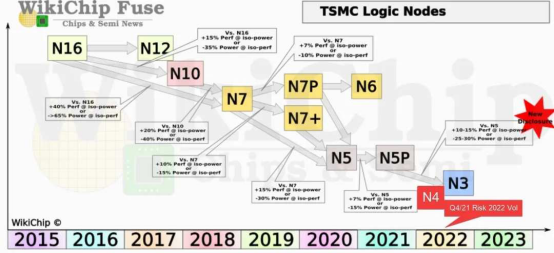
圖 11 臺積電3納米工藝制程芯片預計將在2022年下半年量產
作為目前芯片制造行業的“領頭羊”,臺積電也公布了自己的3納米戰略。2020年4月,臺積電正式披露了其3納米工藝技術細節,晶體管密度高達2.5億/平方毫米。采用臺積電7納米極紫外光刻工藝的麒麟990 5G芯片的晶體管密度約為0.9億/平方毫米,3納米工藝晶體管密度是7納米的3.6倍。在性能提升方面,臺積電5納米比7納米性能提升15%,能耗降低30%。然而,預計3納米比5納米性能提升10%~15%,能耗降低25%~30%;在晶體管密度方面,臺積電表示3納米工藝較5納米提高了1.7倍,晶體管密度高達2.5億/平方毫米。與三星不同,在技術方面,臺積電評估了多種方案,認為現行的鰭式場效應晶體管(FinFET)技術在成本及能效上更佳,首批3納米芯片仍將采用FinFET技術。此外,臺積電還表示,3納米的研發符合預期,并沒有受到疫情影響,預計在2021年進入風險試產階段,2022年下半年正式量產。
九、新型稀土金屬提純方法有望解決美國進口依賴問題
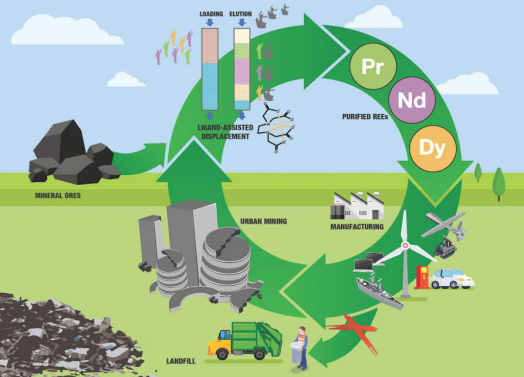
圖 12 使用配體輔助色譜法從煤灰、廢舊磁鐵中提純稀土金屬,確保電子產品關鍵材料的充足供應。(圖片來源:普渡大學)
全球稀土金屬市場總量達40億美元,隨著新電子產品、飛機、艦船、電動汽車的計算機芯片、發動機磁鐵和其他關鍵產品的發展,稀土金屬需求量還在持續增長。但地球上的稀土資源有限,難以確保可持續發展。
2020年5月,美國普渡大學經過10年研發,提出一種具有自主知識產權的提取和凈化工藝——使用配體輔助色譜法從煤灰、廢舊磁鐵和原礦中,安全、有效地凈化和提純稀土金屬,且不影響環境,使美國能夠在國內創造一個更穩定、更可靠的稀土金屬來源。傳統提純稀土元素的方法為兩相液-液萃取法,該工藝需要使用成千上萬個串聯或并聯的混合沉降器單元,同時還會產生大量有毒廢物。普渡大學開發的新工藝使用兩區配體輔助置換色譜系統和一種新的區分離方法,可生產出純度為99%的稀土金屬。研究人員表示,該工藝有望解決美國一直以來因稀土金屬過于依賴進口而產生的供應鏈隱患。
十、人工智能技術推進新材料研發進程
人工智能技術的發展加快了多種材料的成分設計,其中超硬材料和高熵合金的發展成為其中亮點。
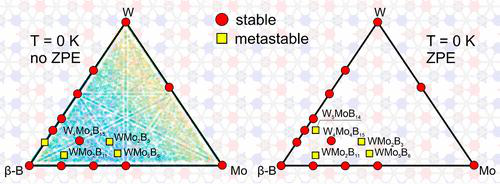
圖 13 W-Mo-B體系在0K時的三元相圖(圖片來源:Skoltech)
2020年9月,俄羅斯斯科爾科沃科學技術學院使用人工智能計算方法成功預測出幾種由鎢、鉬、硼三種主元素組成的新型超硬材料。長期以來,科學家對二元材料進行了深入的研究,性能的進一步提升進入瓶頸期,為了設計新型材料,現在越來越頻繁地加入第三種主元素,以期通過增加材料系統復雜性的方式來提升材料性能。研究人員開發出一種名為USPEX的進化算法(人工智能算法中的一種),成功預測了鎢-鉬-硼材料體系中的超硬三元化合物結構,與二元化合物相比顯示出更好的硬度與斷裂韌性,其中一些材料屬于高熵合金。這項研究為尋找新型超硬硼化物材料奠定了基礎。
高熵合金一般由相等或相似比例的四種或更多元素組成,理論上可以組合出無限種合金組合,并且具有出色的機械、熱、物理和化學性能,目前已開發出多種耐腐蝕、耐高溫、耐低溫、高強度合金。但是新型高熵合金的設計往往基于反復試驗,需要花費大量時間和高額成本。2020年11月,韓國浦項科技大學開發了一種使用人工智能進行高熵合金相位預測的技術。研究團隊開發的人工智能技術在模型優化、數據生成和參數分析等三個方面進行了深度學習,可提高高熵合金相位的可預測性和可解釋性。研究結果有望大大減少現有新材料開發過程所需的時間和成本,未來可用于開發新的高熵合金。
免責聲明:本網站所轉載的文字、圖片與視頻資料版權歸原創作者所有,如果涉及侵權,請第一時間聯系本網刪除。
相關文章
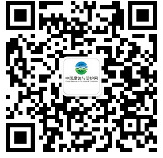
官方微信
《中國腐蝕與防護網電子期刊》征訂啟事
- 投稿聯系:編輯部
- 電話:010-62316606-806
- 郵箱:fsfhzy666@163.com
- 中國腐蝕與防護網官方QQ群:140808414
點擊排行
PPT新聞
“海洋金屬”——鈦合金在艦船的
點擊數:7130
腐蝕與“海上絲綢之路”
點擊數:5741