二氧化碳的臨界溫度為31 ℃,臨界壓力為7.4 MPa。當溫度及壓力超過其臨界點時,二氧化碳將轉變為超臨界二氧化碳(sCO2),其具有傳熱效率高、壓縮性好、無毒無害等特性,是核動力裝置或熱力轉換裝置的潛在工質。在火電系統之中,若以sCO2替代水作為發電介質,發電效率可達50%以上;而在核動力系統之中,若以sCO2代替He作為冷卻劑,在相似的能量轉換效率下,可以降低堆芯出口溫度,降低對材料性能的挑戰。
多家機構對應用于sCO2環境的材料進行了初步篩選與評估,提出了一系列候選材料。sCO2環境中的選材與材料的成分有著密不可分的關系,其中,Cr、Ni及Mn、Mo、Ti、Al等元素含量的差異將會造成氧化膜成分的差別。
800H作為一種高鎳奧氏體合金,在高溫環境下具有較強的耐腐蝕性能和優秀的力學性能,被用于核電廠傳熱管。被視為先進核能系統的sCO2核動力裝置,其運行溫度介于500~700 ℃,這對燃料及結構材料的選型都有著極其嚴格的要求。
上海交通大學聯合中國核動力研究設計院、上海核工程研究設計院有限公司的研究人員以800H合金為研究對象,研究其在高溫(650 ℃)高壓(20 MPa)的sCO2環境中的均勻腐蝕行為,為800H合金在sCO2環境中的應用提供參考。
1 試驗方案
試驗材料為商用800H合金,通過線切割方法將800H合金加工成片狀的均勻腐蝕試樣,試樣尺寸為20 mm×10 mm×2mm。試驗前,試樣表面依次用180號、400號、800號、1200號、2000號碳化硅水砂紙進行打磨。打磨后的試樣首先經超純水沖洗,再將其放入無水乙醇中進行超聲去污,最后對試樣進行烘干處理。
試驗在高溫高壓氣體試驗回路中進行,該試驗回路主要由氣體供給系統、高溫試驗系統和數據采集與控制系統三部分組成,如圖1所示。其中,高壓釜由625鎳基合金制成,容積約為3 L。試驗溫度為650 ℃,壓力為20 MPa,試驗介質為高純度CO2(純度為99.99%)。試驗前,多次循環抽真空并充入CO2以除去釜內氣體雜質。
圖1 高溫高壓氣體試驗回路
試驗主要采用稱量法和微觀分析法對材料腐蝕行為進行表征。試驗前通過游標卡尺測量試樣尺寸計算表面積,并在干燥環境中使用精度為0.1 mg的電子天平進行質量稱量。試驗總時長為1000 h,分別在100、300、500、1000 h時取樣,對試樣進行稱量并記錄,獲得4個腐蝕質量增加數據點。研究表明,310、800H等金屬材料在超臨界二氧化碳環境中的腐蝕質量增加近似滿足拋物線生長規律,因此,可以由公式ΔW=ktn對800H合金的腐蝕質量增加進行擬合。式中k為氧化速率常數,g/(m2·s);t為腐蝕時間,s;ΔW為材料單位面積上的質量增加,g/m2;n為試樣氧化動力學參數。
采用掃描電鏡、能譜儀、X射線衍射儀對腐蝕不同時間后試樣表面進行觀察和分析。
2 試驗結果與討論
腐蝕質量增加
在650 ℃/20 MPa的sCO2環境中腐蝕不同時間后800H合金的質量增加如圖2所示。根據上式對圖2中曲線進行擬合,得到曲線方程ΔW=0.002167t0.42,其擬合精度R2=0.95。
圖2 在650 ℃/20 MPa的sCO2環境中腐蝕不同時間后800H合金的質量增加
由上述方程可知,在650 ℃/20 MPa的sCO2環境中800H合金的氧化速率常數為0.002167 g/(m2·s),其質量增加速率較低。由腐蝕質量增加曲線可知,當腐蝕時間達到1000 h時,800H合金的質量增加為11.2 mg/dm2,小于相同腐蝕條件下310不銹鋼(約15 mg/dm2)及316不銹鋼(約100 mg/dm2)的腐蝕質量增加量,這說明800H合金耐腐蝕性能優異。在腐蝕試驗的前100 h內,800H合金的質量增加速率較快;腐蝕試驗進行至300 h時,質量增加量約為9.3 mg/dm2,占總增量的83%;之后,質量增加曲線趨于平緩。這說明試驗進行了300 h后,800H合金表面的氧化膜對氧向基體內部的擴散和基體金屬元素向外界的遷移起到了一定的抑制作用。
表面氧化膜形貌
利用掃描電鏡對在650 ℃/20 MPa的sCO2環境中腐蝕100、300、500、1000 h試樣表面氧化膜的形貌進行觀察和分析,結果如圖3所示。800H合金在sCO2環境中腐蝕100 h后,其表面生成了一層連續的顆粒狀氧化膜,氧化物顆粒間仍存在孔洞、縫隙等缺陷(圖3中箭頭標識區域)。該層氧化膜在一定程度上減弱了基體與腐蝕介質間的元素擴散,但氧化物顆粒間的孔洞、縫隙等缺陷為元素擴散提供了通道。結合800H合金的腐蝕質量增加曲線可知,試驗進行到300 h時,其腐蝕速率才趨近于平緩。800H合金表面形成的氧化物顆粒的尺寸隨著腐蝕時間的延長而逐漸增大,其分布變得更加密集。當腐蝕500~1000 h時,800H合金表面氧化物形貌和尺寸沒有發生明顯的變化,說明氧化物生長速率降低。腐蝕1000 h后,氧化物顆粒之間出現粘連,粘連處出現尺寸較小的氧化物顆粒,說明此時仍然有一定數量的氧化物在合金表面形成,且生長速率較為緩慢。
圖3 在650 ℃/20 MPa的sCO2環境中腐蝕不同時間后800H合金表面氧化膜形貌
圖4為800H合金在650 ℃/20 MPa的sCO2環境中腐蝕500 h后表面氧化膜的XRD譜。從圖4中可以發現,奧氏體相的特征峰在整個XRD譜圖中占有最高的強度,這說明800H合金表面生成的氧化膜厚度較薄。除奧氏體特征峰外,XRD還檢測到了較微弱的Cr2O3的特征峰,說明表面氧化膜的主要成分為Cr的氧化物Cr2O3。
圖4 在650 ℃/20 MPa的sCO2環境中腐蝕500 h后800H合金表面氧化膜的XRD譜
表面缺陷
在650 ℃/20 MPa的sCO2環境中腐蝕500 h和1000 h試樣表面選取典型區域進行EDS點掃,并對點掃結果進行歸一化處理,分析位置見圖5,分析結果見表1。
圖5 在650 ℃/20 MPa的sCO2環境中腐蝕500 h與1000 h的800H合金表面EDS分析位置
表1 800H合金基體及腐蝕不同時間后表面不同位置的化學成分
由圖5(a)可見,在650 ℃/20 MPa的sCO2環境中腐蝕500 h后,800H合金表面附著一層均勻的氧化物,但在部分區域(區域1、區域2)出現了深色圓孔,這可能是表面缺陷或腐蝕過程中形成的孔洞。由表2可見,點1、點2處(均勻氧化膜上)Cr元素含量均要高于基體部分,說明在表面形成的氧化膜中富含Cr元素,這與XRD分析結果相對應。
由圖5(b)、(c)可見,腐蝕1000 h后,800H合金表面出現了不同種類的缺陷。對比點1、點2與點3的元素成分,發現隨著腐蝕時間的延長,Cr元素的含量隨之增加,而Fe、Ni元素的含量降低,這說明在800H合金表面富Cr氧化物的厚度逐漸增加。點4處的氧化物顆粒尺寸明顯大于點3處,其形狀仍為多邊體,但較為稀疏。點5、點6處出現的白色不規則顆粒物中Cr含量要遠高于表面均勻氧化膜。點7、點8為缺陷周邊的取樣點,該處Cr的含量比均勻氧化膜處有一定的增加,而相對于基體材料顯著升高。
截面形貌
用掃描電鏡觀察在650 ℃/20 MPa的sCO2環境中腐蝕300 h后800H合金的截面形貌,并用EDS對試樣截面進行線掃,分析氧化物和基體成分,結果見圖6。
圖6 在650 ℃/20 MPa的sCO2環境中腐蝕300 h后800H合金截面的SEM圖及EDS線掃結果
由圖6可知,在650 ℃/20 MPa的sCO2環境中腐蝕300 h后,800H合金基體表面形成了連續且致密的氧化膜,氧化膜平均厚度約為500 nm。氧化膜中Cr元素含量遠高于基體部分Cr含量,結合XRD結果進一步確認了材料表面生成的氧化膜主要成分為Cr2O3。連續且致密的Cr2O3將減緩材料基體與腐蝕介質的元素交換,提高材料的耐蝕性。此外,氧化膜下方的基體中存在一定厚度的貧Cr區,該區域Cr含量低于基體內部區域Cr含量,其產生原因主要為該區域Cr元素的向外擴散;在氧化膜表面C含量較高,且沿著氧化膜向基體方向逐漸減少。
用掃描電鏡觀察在650 ℃/20 MPa的sCO2環境中腐蝕1000 h后800H合金的截面形貌,并用EDS面掃描分析元素分布情況,結果見圖7。結果表明,在650 ℃/20 MPa的sCO2環境中腐蝕1000 h后,800H合金表面氧化膜厚度為1~4 μm。EDS面掃結果顯示,表面氧化物主要成分富Cr。這與腐蝕300 h后截面線掃結果相吻合,僅在氧化膜表面發現較高含量的C。
圖7 在650 ℃/20 MPa的sCO2環境中腐蝕1000 h后800H合金截面形貌及元素分布圖
在sCO2中,碳的沉積主要通過Boudouard反應實現;CO主要來源于金屬與環境中CO2的反應。
EDS面掃結果顯示,C元素在氧化膜表面的含量較高。其原因可能是CO2在金屬表面發生了還原反應,導致C沉積于氧化膜表面。另外,Al和Si元素存在于氧化膜與基體(O/M)交界面。研究表明,800H合金的氧化膜中存在較薄的SiO2將有效降低材料在sCO2環境中的腐蝕,而800H合金中Al元素形成的Al2O3進一步促進了合金表面氧化物的形成。圖7中Al與Si元素在O/M交界面具有較高的富集程度,結合O元素分布可知在O/M界面處可能生成了Al2O3和SiO2氧化物。而該種現象的產生,主要是由于Si、Al元素相比于Fe、Cr等元素具有著更高的親氧性,它們將優先形成氧化物并富集于O/M界面處。其中,Si元素的富集程度最為明顯,這進一步提升了材料的耐腐蝕性能。
結論
(1) 800H合金在650 ℃/20 MPa的sCO2環境中的腐蝕質量增加隨時間近似服從拋物線生長規律,腐蝕1000 h后質量增加11.2 mg/dm2。
(2) 800H合金表面氧化膜的主要成分是Cr2O3,其結構致密且具有保護性。富Cr氧化膜的厚度隨腐蝕時間的延長而增加,腐蝕1000 h后氧化膜厚度為1~4 μm,且氧化膜表面出現C元素的沉積。
(3) 氧化膜與基體交界面出現了富Al氧化物及富Si氧化物,這是材料的耐腐蝕性能進一步提升的主要原因之一。
免責聲明:本網站所轉載的文字、圖片與視頻資料版權歸原創作者所有,如果涉及侵權,請第一時間聯系本網刪除。
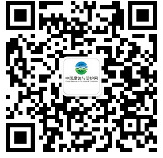
官方微信
《腐蝕與防護網電子期刊》征訂啟事
- 投稿聯系:編輯部
- 電話:010-62316606
- 郵箱:fsfhzy666@163.com
- 腐蝕與防護網官方QQ群:140808414