通常我們通過手冊(cè)所獲得的S-N曲線大多是無缺口的標(biāo)準(zhǔn)試樣的試驗(yàn)結(jié)果,但是實(shí)際零部件的形狀、尺寸、表面狀態(tài)、工作環(huán)境和工作載荷的特點(diǎn)都可能大不相同,而這些因素都對(duì)零部件的疲勞強(qiáng)度產(chǎn)生很大的影響。疲勞強(qiáng)度的影響因素可分為力學(xué)、冶金學(xué)和環(huán)境三個(gè)方面。這些因素互相聯(lián)系影響,使得在疲勞強(qiáng)度設(shè)計(jì)和疲勞壽命預(yù)測(cè)時(shí),綜合評(píng)價(jià)這些因素影響變得復(fù)雜。
三類因素中,力學(xué)因素從根本上講可歸結(jié)為應(yīng)力集中和平均應(yīng)力的影響;冶金學(xué)因素可歸納為冶金質(zhì)量即材料的純凈度和材料的強(qiáng)度;而環(huán)境因素主要有腐蝕介質(zhì)和高溫的影響。對(duì)于鐵路車輛零部件大多數(shù)的情況是在大氣和常溫環(huán)境下工作的,所以一般情況下應(yīng)主要考慮力學(xué)和冶金學(xué)兩類因素。它們包括缺口形狀的影響、尺寸的影響、表面狀態(tài)的影響和平均應(yīng)力的影響等。關(guān)于這些因素對(duì)疲勞極限影響的具體數(shù)據(jù)相關(guān)的經(jīng)驗(yàn)公式,可查閱有關(guān)手冊(cè)和資料。這里主要討論疲勞強(qiáng)度設(shè)計(jì)和疲勞壽命預(yù)測(cè)時(shí)需要了解的一些比較重要的影響規(guī)律或現(xiàn)象,以及必須或應(yīng)該考慮到的注意事項(xiàng)。
PART.01 缺口形狀效應(yīng)
零件或構(gòu)件常常帶有如軸肩類的臺(tái)階、螺栓孔和油孔、鍵槽等所謂的缺口,它們的共同特點(diǎn)是零件的橫截面積在缺口處發(fā)生了突變,而在這些缺口根部應(yīng)力會(huì)急劇升高,這種現(xiàn)象叫做應(yīng)力集中。
缺口處的應(yīng)力集中是造成零部件疲勞強(qiáng)度大幅度下降的最主要的因素。應(yīng)力集中使得缺口根部的實(shí)際應(yīng)力遠(yuǎn)大于名義應(yīng)力,使該處產(chǎn)生疲勞裂紋,最終導(dǎo)致零件失效或破壞。應(yīng)力集中的程度用應(yīng)力集中系數(shù)(又稱理論應(yīng)力集中系數(shù))Kt 來描述,表達(dá)式如下:
這里,σmax為最大應(yīng)力,σ0為載荷除以缺口處凈截面積所得平均應(yīng)力,又稱名義應(yīng)力。
在一定范圍內(nèi),缺口根部的曲率半徑ρ 越小,應(yīng)力集中程度越大,疲勞強(qiáng)度降低的程度也就越大。但是,對(duì)于低中碳鋼等塑性材料,當(dāng)缺口根部的曲率半徑進(jìn)一步減小甚至小于零點(diǎn)幾個(gè)毫米時(shí),疲勞強(qiáng)度的降低程度會(huì)變的越來越小甚至不再降低。此時(shí)應(yīng)力集中系數(shù)就無法真實(shí)地反映缺口對(duì)疲勞強(qiáng)度的影響。因此常用疲勞缺口系數(shù)Kf(fatigue notch factor,過去又被稱為有效應(yīng)力集中系數(shù))來更直接地反映疲勞強(qiáng)度的真實(shí)的降低程度。
這里,σw0,σw分別為無缺口光滑試樣和缺口試樣的疲勞極限。
下圖為鋼的應(yīng)力集中系數(shù)Kt與疲勞缺口系數(shù)Kf之間的關(guān)系。由圖可見,對(duì)于低中碳鋼,在應(yīng)力集中系數(shù)小于2~2.5時(shí)Kt與Kf基本相同,但當(dāng)超過此數(shù)值時(shí),Kf的增長(zhǎng)速度明顯變慢。而對(duì)于高碳鋼等強(qiáng)度比較高的鋼,Kf隨Kt 線性遞增的關(guān)系保持很長(zhǎng)的范圍。由此可知,高強(qiáng)度鋼的疲勞強(qiáng)度對(duì)缺口的敏感性高而低中強(qiáng)度鋼的疲勞強(qiáng)度對(duì)缺口的敏感性較低。
一般情況下,Kf<Kt,但對(duì)于高碳鋼尖銳缺口,還有可能存在Kt >Kf的現(xiàn)象。對(duì)于螺栓類零件也存在這種現(xiàn)象,有時(shí)出現(xiàn)Kt為約4左右而Kf為8~10的情況。這主要是因?yàn)槊總€(gè)螺紋所分擔(dān)的載荷不均,甚至載荷幾種在某扣螺紋上所致。
對(duì)于光滑材料,通過表面淬火、表面滲碳、表面氮化等表面熱處理可以有效地提高其疲勞強(qiáng)度。但是對(duì)于缺口材料,這些方法可能變的沒有效果甚至使疲勞強(qiáng)度反而降低。這是因?yàn)橥ㄟ^熱處理使其表面強(qiáng)度提高的同時(shí),使缺口敏感性也變高的緣故。
下圖為高強(qiáng)度鋼和塑性較好的低強(qiáng)度鋼的缺口材料的疲勞強(qiáng)度隨應(yīng)力集中程度的增加而變化的情況。在應(yīng)力集中Kt較小的范圍內(nèi),高強(qiáng)度鋼的疲勞強(qiáng)度明顯比低強(qiáng)度鋼的高。但隨著應(yīng)力集中系數(shù)的增加,高強(qiáng)度鋼的疲勞強(qiáng)度的降低速度明顯大于低強(qiáng)度鋼者,以致于高強(qiáng)度鋼的疲勞強(qiáng)度與低強(qiáng)度鋼的疲勞強(qiáng)度相差無幾。
對(duì)于焊接構(gòu)件,由于焊接熱影響區(qū)在許多情況下恰好處于結(jié)構(gòu)性缺口部位或在其附近,加之焊接缺陷、焊接殘余拉應(yīng)力的作用等,使得疲勞強(qiáng)度可能大幅下降幾倍甚至十幾倍。
疲勞缺口系數(shù)還受零部件尺寸大小的影響,一般地在具有相同缺口的情況下,隨著尺寸的增大其疲勞缺口系數(shù)也有所增大。
因此對(duì)于缺口材料或帶有缺口的零部件,為了提高其疲勞壽命,最有效的方法是合理地進(jìn)行結(jié)構(gòu)設(shè)計(jì)和工藝選擇等手段,來設(shè)法降低或改進(jìn)它的應(yīng)力集中情況。而一味地選用高強(qiáng)度鋼材,未必能夠達(dá)到目的,相反在表面較粗糙和尺寸較大的情況下有可能反而使構(gòu)件的疲勞強(qiáng)度下降。
PART.02 零件尺寸效應(yīng)
用于疲勞試驗(yàn)的式樣的直徑一般都在5~10mm的范圍內(nèi),這和實(shí)際零部件的尺寸有很大的差異。一般地,對(duì)于彎曲和扭轉(zhuǎn)載荷下的零件,隨著尺寸的增大疲勞強(qiáng)度降低。但是對(duì)于軸向拉伸和壓縮載荷的情況,尺寸大小的影響不大。尺寸對(duì)疲勞極限影響的大小用尺寸影響系數(shù)ε來表示。
這里,σd、σd0分別為任意尺寸和標(biāo)準(zhǔn)尺寸光滑試樣的疲勞極限。
高強(qiáng)度鋼的尺寸效應(yīng)比低強(qiáng)度鋼的尺寸效應(yīng)大,表面粗糙的零件的尺寸效應(yīng)較大。
尺寸效應(yīng)的產(chǎn)生主要是因?yàn)?,較大尺寸的材料的組織狀態(tài)和應(yīng)力梯度對(duì)疲勞強(qiáng)度產(chǎn)生了影響。材料的尺寸越大制造工藝過程越難控制,材料組織的致密性和均勻性等越差、冶金缺陷越多,表面積越大這些缺陷的數(shù)量也越多,因此大尺寸試樣表面產(chǎn)生疲勞、裂紋的機(jī)會(huì)也就越大。而這些從根本上來說又都可以歸結(jié)為冶金缺陷造成了局部應(yīng)力集中而導(dǎo)致了疲勞裂紋的產(chǎn)生。
關(guān)于應(yīng)力梯度的影響,在承受彎曲、扭轉(zhuǎn)等載荷的情況下,零件的尺寸越大工作應(yīng)力的梯度越小,單位面積內(nèi)的平均應(yīng)力就越高,疲勞裂紋越易產(chǎn)生。
PART.03 表面狀況的影響
表面狀況包括表面粗糙度、表面應(yīng)力狀態(tài)、表面塑性變形程度和表面缺陷等因素,在試驗(yàn)中采用的是表面磨光(或拋光)的標(biāo)準(zhǔn)試樣,但實(shí)際的零部件的表面則往往是機(jī)械加工表面鍛造表面和鑄造表面。
機(jī)械加工會(huì)在零件表面產(chǎn)生塑性加工硬化。切削加工往往會(huì)在零件表面產(chǎn)生一定的殘余壓應(yīng)力,這對(duì)疲勞強(qiáng)度是有利的但效果有限。但是,在磨削時(shí)往往會(huì)產(chǎn)生對(duì)疲勞強(qiáng)度不利的殘余拉應(yīng)力。另一方面,機(jī)械加工表面的顯微尺度上的凸凹不平引起應(yīng)力集中而使疲勞強(qiáng)度降低。這些因素綜合作用的結(jié)果,使疲勞強(qiáng)度比標(biāo)準(zhǔn)試樣的要降低一些。而鍛造或鑄造表面一般具有更高的表面粗糙度,且存在表面加工硬化層和表面殘余壓應(yīng)力,因此會(huì)更加明顯地降低疲勞強(qiáng)度。因此從形式上看,越是粗糙的表面加工方法,對(duì)疲勞強(qiáng)度的降低影響就越大。表面加工狀況對(duì)疲勞強(qiáng)度的影響用表面加工系數(shù)β來表示。
這里,σβ為某種表面狀態(tài)下標(biāo)準(zhǔn)光滑試樣的疲勞極限,σβ0為磨光標(biāo)準(zhǔn)光滑試樣的疲勞極限,國外為表面磨光的標(biāo)準(zhǔn)光滑試樣。
從冶金角度看,粗加工對(duì)高強(qiáng)度材料的疲勞強(qiáng)度的影響更大,以至于在粗加工狀態(tài)下高強(qiáng)度鋼可能起不到絲毫提高疲勞強(qiáng)度的作用。這主要是因?yàn)楦邚?qiáng)度材料對(duì)粗糙表面的缺口敏感性高的緣故,加之機(jī)械加工對(duì)于高強(qiáng)度鋼的表面的加工硬化作用也很小。
關(guān)于表面脫碳、表面碰磕傷痕和劃傷等表面缺陷等,對(duì)疲勞強(qiáng)度的影響的研究較少,但這些偶然原因造成的表面缺陷會(huì)對(duì)疲勞強(qiáng)度造成很大的影響。因此,在設(shè)計(jì)尤其是制造過程中需要給予足夠的重視。
對(duì)于光滑材料,表面熱處理等表面改性方法可以提高疲勞強(qiáng)度,但對(duì)于實(shí)際零部件等帶有缺口的材料,這些方法都效果不大,甚至產(chǎn)生相反的作用。因此多用噴丸、輥壓的方法使表面產(chǎn)生加工硬化和殘余壓應(yīng)力,從而提高構(gòu)件的疲勞強(qiáng)度,但是這兩種方法一般對(duì)孔口類缺口的零件的疲勞強(qiáng)度的提高作用并不明顯。
最新的研究表明,用簡(jiǎn)單的金屬模具對(duì)孔口邊緣進(jìn)行少量倒角,從而使缺口部位殘生局部塑性變形的方法,對(duì)疲勞強(qiáng)度有明顯的提高,甚至可以完全消除缺口降低疲勞極限的影響。過去大多認(rèn)為,表面塑性加工的方法提高疲勞強(qiáng)度的主要原因是在表面產(chǎn)生了殘余壓應(yīng)力從而抵消了部分工作應(yīng)力的緣故。實(shí)際上是殘余壓應(yīng)力在缺口部位產(chǎn)生的壓縮集中應(yīng)力抵消了缺口的不利影響;塑性變形使得缺口附近組織中的微小薄弱區(qū)域得到強(qiáng)化,使組織性能變的更加均勻一致,整體強(qiáng)度得到提高,從而使產(chǎn)生疲勞裂紋的應(yīng)力水平得到提高。同時(shí),殘余壓應(yīng)力還使疲勞裂紋擴(kuò)展停止而成為停留裂紋。
PART.04 平均應(yīng)力的影響
如前所述,產(chǎn)生疲勞破壞的根本原因是動(dòng)應(yīng)力分量,但靜應(yīng)力分量即平均應(yīng)力對(duì)疲勞極限也有一定的影響。在一定的靜應(yīng)力范圍內(nèi),壓縮的靜應(yīng)力提高疲勞極限,拉伸的靜應(yīng)力降低疲勞極限。一般認(rèn)為,殘余應(yīng)力對(duì)疲勞極限的作用同平均應(yīng)力的作用相同。對(duì)一種材料, 可根據(jù)它在各種平均應(yīng)力或應(yīng)力比R下的疲勞極限結(jié)果畫出疲勞極限圖。
下圖的橫坐標(biāo)為平均應(yīng)力σm(或殘余應(yīng)力)和強(qiáng)度極限σb的比值,縱坐標(biāo)為應(yīng)力幅σa和對(duì)稱循環(huán)疲勞極限σ-1的比值,兩者都是無量綱的量。
從圖中可以看出,多數(shù)試驗(yàn)數(shù)據(jù)點(diǎn)落在直線與曲線之間。這條直線稱為古德曼 (Goodman) 線;曲線就是杰柏 (Gerber) 拋物線;用屈服極限σs 代替σb 得到索德柏格 (Soderberg) 線;用斷裂真應(yīng)力σf 代替σb,得到摩儒 (Morrow) 線。如下:
Goodman 線:
Gerber 線:
Soderberg 線:
Morrow 線:
古德曼 (Goodman) 線對(duì)于延性金屬略偏保守且簡(jiǎn)單方便,在疲勞設(shè)計(jì)中應(yīng)用最廣。常用的還有另一種叫做理想的改進(jìn)Goodman圖。下圖為工字形型鋼對(duì)接梁彎曲疲勞載荷下理想的改進(jìn)Goodman圖。橫坐標(biāo)表示最小應(yīng)力σmin,縱坐標(biāo)表示最大應(yīng)力σmax,其直線方程式為
式中,m 是Goodman線的斜率,b 為直線在y軸上的截距,它是最小應(yīng)力等于零時(shí)即脈動(dòng)循環(huán)的疲勞極限。疲勞極限用最大應(yīng)力表示時(shí),即σw=σmax,考慮到應(yīng)力比R=σmax/σmin,由Morrow 線有
由上式即可求出應(yīng)力比為R 時(shí)的疲勞極限。實(shí)際車輛的具體結(jié)構(gòu)要遠(yuǎn)比獲得S-N曲線時(shí)的試驗(yàn)條件復(fù)雜,例如焊接形式及應(yīng)力集中等等,美國AAR標(biāo)準(zhǔn)為我們提供了許多典型焊接結(jié)構(gòu)疲勞強(qiáng)度方面的有價(jià)值的參考,所以,實(shí)際計(jì)算中的b與m均取自于AAR標(biāo)準(zhǔn)。
試驗(yàn)研究表明,靜載分量對(duì)應(yīng)力集中系數(shù)、尺寸系數(shù)、表面系數(shù)的影響較小,可以忽略。
免責(zé)聲明:本網(wǎng)站所轉(zhuǎn)載的文字、圖片與視頻資料版權(quán)歸原創(chuàng)作者所有,如果涉及侵權(quán),請(qǐng)第一時(shí)間聯(lián)系本網(wǎng)刪除。
-
標(biāo)簽: 疲勞強(qiáng)度, 因素, 綜合評(píng)價(jià)
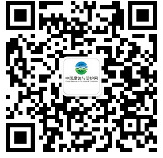
官方微信
《腐蝕與防護(hù)網(wǎng)電子期刊》征訂啟事
- 投稿聯(lián)系:編輯部
- 電話:010-62316606-806
- 郵箱:fsfhzy666@163.com
- 腐蝕與防護(hù)網(wǎng)官方QQ群:140808414