近些年來,我國在材料領(lǐng)域的基礎(chǔ)研究取得了非常大的進(jìn)步。據(jù)不完全統(tǒng)計,我國在2019年的論文數(shù)就超越了美國,遙遙領(lǐng)先于其他國家。但是,論文數(shù)量僅僅是材料領(lǐng)域進(jìn)步的冰山一角,解決重大工程的掐脖子問題并將其應(yīng)用在大國重器上才是一個國家進(jìn)步的根本體現(xiàn)。在國家最新的十四五規(guī)劃中,科技部和工信部已經(jīng)把解決“卡脖子”技術(shù)列入了重要研發(fā)項目之中。同時,清華大學(xué),上海交大,西工大等全國985著名高校正式將 “破五唯”體制列入規(guī)劃。由此可見,以論文論英雄的時代即將結(jié)束,取而代之的則是代表作、成果轉(zhuǎn)化以及科技產(chǎn)業(yè)經(jīng)濟(jì)化。其實,近些年來,我國在“國之大器”,“卡脖子”等技術(shù)問題上還是取得了不少突破,有些打破了國外壟斷,有些則是首創(chuàng),達(dá)到了國際先進(jìn)或者領(lǐng)先水平。筆者今天給大家分享的正是這些花費科學(xué)家無數(shù)心血,但可歌可泣的技術(shù)以及背后的故事。
1)中國科學(xué)院金屬研究所李依依院士,李殿中和孫明月等人在國際上率先制備無焊縫整體不銹鋼大環(huán)
第四代核電具有許多優(yōu)點,例如安全可靠,能源利用效率高且可持續(xù)性發(fā)展,許多國家,如美國、法國、日本等正在加快第四代核反應(yīng)堆的建設(shè)。建造超大型核反應(yīng)堆的需要相應(yīng)地結(jié)構(gòu)材料,其中一個關(guān)鍵問題是用于制造反應(yīng)堆部件的重型工程結(jié)構(gòu)的實用性。支撐環(huán)是反應(yīng)堆的關(guān)鍵重型結(jié)構(gòu)部件,可支撐整個反應(yīng)堆容器和內(nèi)部的7000多噸重量。此外,它也是反應(yīng)堆容器的邊緣,在工作條件下會承受高壓,高溫以及其他颶風(fēng)荷載,地震荷載和靜荷載。因此,支撐環(huán)的安全性和穩(wěn)定性對于核反應(yīng)堆至關(guān)重要。由于支撐環(huán)的最大直徑可達(dá)15.6 m,因此理論上將消耗200噸以上的不銹鋼。但是按照目前的冶煉技術(shù),要實現(xiàn)他的一體成型技術(shù),做出不含成分偏析、縮松和縮孔等缺陷的大環(huán)材是不可能的。以前,最常用的方法是制造焊接類型的支撐環(huán),但是由于多次縱向焊接,支撐環(huán)的安全性和穩(wěn)定性將大打折扣。這會造成材料的壽命縮短,嚴(yán)重造成資源浪費,給四代核電的發(fā)展形成空前的挑戰(zhàn)。中國科學(xué)院金屬研究所李依依院士,李殿中和孫明月研究員等人獨辟蹊徑,在全球率先發(fā)明金屬構(gòu)筑成形技術(shù)。該技術(shù)以多塊小尺寸均質(zhì)化板坯作為基元,通過表面活化 、真空封裝、高溫形變等手段,使構(gòu)筑界面與基體完全一致,進(jìn)而獲得大鍛件所需均質(zhì)化母材,實現(xiàn)“以小制大”的新型制造。實現(xiàn)了世界上最大的整體式無焊支撐環(huán)(φ= 15.6 m)構(gòu)筑成型。與必須通過較大的毛坯進(jìn)行重型鍛造的傳統(tǒng)觀念形成鮮明對比的是,該技術(shù)的核心思想是通過建造更小,更便宜的金屬板來制造大型的高質(zhì)量零件。在這個巨型環(huán)上,根本不存在所謂的焊縫,整體性能得到了顯著提升,已經(jīng)成功的運用于我國的第四代核電站反應(yīng)堆制造,取得了顯著的經(jīng)濟(jì)效益。得到了多位院士專家及企業(yè)的認(rèn)可,并被評價為大構(gòu)件制造領(lǐng)域的一項變革性技術(shù)。該技術(shù)具有低成本、高品質(zhì)、質(zhì)量穩(wěn)定及綠色環(huán)保等優(yōu)勢,成為當(dāng)前大環(huán)件制造的一種重要新興技術(shù)。然而,雖然金屬構(gòu)筑技術(shù)能夠制造高品質(zhì)大型鍛件鋼坯,但由于該技術(shù)需要采用真空電子束封焊,對于一些難焊、不可焊金屬,采用構(gòu)筑技術(shù)則不能實現(xiàn)。該技術(shù)入選“共和國成就發(fā)展巡禮”,在央視多次播出。未來,這項技術(shù)有望解決艦船、核電、航天等戰(zhàn)略性裝備核心部件制造的難題,使我國工業(yè)發(fā)展實現(xiàn)質(zhì)的飛躍。
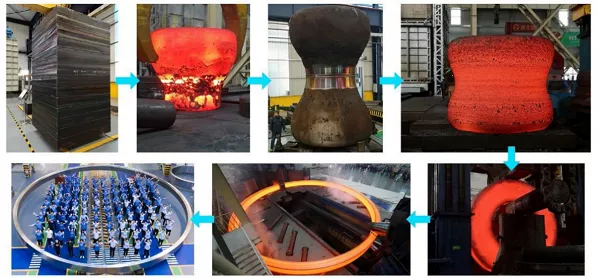
圖1 采用多層熱壓粘結(jié)法制造無焊縫不銹鋼鍛造環(huán)的工藝。首先對316不銹鋼鑄坯表面進(jìn)行清理、整齊堆放,然后用電子束焊機(jī)進(jìn)行真空封裝。然后對整個包體進(jìn)行熱壓粘合,界面完全愈合后成型為初始坯料形狀進(jìn)行二次熱壓粘合。接下來,兩個初始的鋼坯再被電子束焊機(jī)真空包裝,然后熱壓結(jié)合成環(huán)軋制所需的大鋼坯。隨后進(jìn)行沖孔、拉削、軋制,最終得到一個完整的支撐環(huán)[1]。
2)金屬所楊銳教授突破TiAl航空發(fā)動機(jī)葉片一體成型技術(shù)
航空發(fā)動機(jī)是飛機(jī)的心臟,而渦輪葉片又是發(fā)動機(jī)的心臟。這款心臟的動力往往取決于制備它的材料是否過關(guān)。目前,航空發(fā)動機(jī)的壓氣機(jī)和低壓渦輪輪葉片采用的是鎳基高溫合金。這種合金在600-1000℃范圍之類具有較高的強(qiáng)度和耐蝕性,但鎳的密度大,質(zhì)量重。眾所周知,減重是航空工業(yè)一直追求的目標(biāo)。我國首款五代機(jī)殲20總師楊偉曾說過,減重飛機(jī)一克價值一兩黃金。由此可見,減重在航空工業(yè)是多么的重要。相較而言,鈦鋁合金的密度僅為鎳基高溫合金的一半,而且在650-850℃的服役溫度范圍內(nèi),具有更優(yōu)異的力學(xué)性能,讓其替代鎳基高溫合金則會大幅度的實現(xiàn)發(fā)動機(jī)的減重,提高飛機(jī)能源利用率(約為30%)。因此,用鈦鋁合金做發(fā)動機(jī)葉片一直是國內(nèi)外航空發(fā)動機(jī)生產(chǎn)商的追求。為了降低成本,還要求葉片一體成型。而鈦的活性極強(qiáng),只有氧化釔一種材料可以作為制作葉片的容器,可這種材料表面是粉末狀的,會影響葉片精度,德國科學(xué)家甚至通過計算機(jī)模擬得出結(jié)論,這是不可能完成的任務(wù)。中國科學(xué)院金屬研究所研究員楊銳帶領(lǐng)多個學(xué)科的科學(xué)家,歷經(jīng)10年的時間,經(jīng)過無數(shù)次失敗之后,終于成功調(diào)制出一種粘結(jié)劑,解決了鈦鋁合金葉片的容器問題,成功了實現(xiàn)葉片一體澆筑成型,完成了這個不可能完成的任務(wù)。他們終于破解讓氧化釔不再掉渣的難題,一體成型的鈦鋁合金葉片也隨之誕生。雖然這只是一個開端,但讓中國人有勇氣展望未來屬于自己的航空發(fā)動機(jī)。
3)西工大劉東團(tuán)隊強(qiáng)力旋軋技術(shù)(PTR)破解國內(nèi)高端軸承鋼難題
從汽車、高鐵、飛機(jī)到儀器儀表、機(jī)械裝備,你幾乎能從所有旋轉(zhuǎn)的機(jī)械中尋找到一個共同的核心部件——軸承。而制造軸承所需的材料——軸承鋼,被譽(yù)為“鋼中之王”。一直以來,高質(zhì)量的軸承鋼的生產(chǎn)技術(shù)被國外巨頭卡脖子。很多國內(nèi)企業(yè)無法從國內(nèi)廠家尋求到符合高使用需求的軸承鋼,不得不花高價進(jìn)口,這使得他們叫苦連連。擁擠自主產(chǎn)權(quán)的核心技術(shù),擺脫對國外的依賴,一直是人們的愿望。雖然我國很早就已經(jīng)成為了“鋼鐵大國”,但是距離“鋼鐵強(qiáng)國”的夢想還有一段路要走。一直以來,我國所生產(chǎn)的軸承鋼質(zhì)量與國際先進(jìn)水平有較大差距。以夾雜物為例,國外產(chǎn)品夾雜物尺寸完全小于等于10微米,而國內(nèi)最大粒徑達(dá)到50-52μm,大小相差五倍之多。軸承的工作環(huán)境嚴(yán)峻而復(fù)雜,不僅需要高速穩(wěn)定的旋轉(zhuǎn),而且還要承受強(qiáng)力的擠壓、摩擦,甚至超高溫的歷練。因而對軸承鋼的質(zhì)量和可靠性提出了更為嚴(yán)苛的要求。就在今年,西北工業(yè)大學(xué)材料學(xué)院劉東教授和其團(tuán)隊研發(fā)的強(qiáng)力旋軋技術(shù)(PTR),打破國外巨頭技術(shù)壟斷,突破我國軸承鋼“卡脖子”技術(shù),成功了破解行業(yè)難題。如何生產(chǎn)高質(zhì)量的軸承鋼?一是內(nèi)部足夠純凈,夾雜物質(zhì)越少越好;二是足夠均勻,材料內(nèi)的顆粒物盡量細(xì)小、彌散。“強(qiáng)力旋軋技術(shù)”利用曼內(nèi)斯曼效應(yīng),在徑向軋制的同時施加強(qiáng)力旋轉(zhuǎn),依靠連續(xù)局部壓扭復(fù)合變形,實現(xiàn)軸承管材碳化物均勻細(xì)小彌散。就像在揉面的時候讓面的3個方向都變形,而且變形數(shù)值非常大,這樣就可以把面揉的又透又勁道。劉東教授和團(tuán)隊“十年磨一劍”,經(jīng)過不斷攻關(guān)測試,終于突破技術(shù)瓶頸,研究出3個世界首創(chuàng),申請到66項發(fā)明專利,強(qiáng)力旋軋技術(shù)就是其中一項。運用強(qiáng)力旋軋(PTR)技術(shù),晶粒尺寸可由原來的50μm細(xì)化至10μm,碳化物尺寸僅為原先的1/10。首次將100年來,一直徘徊在600-700HV的GCr15軸承鋼硬度提高至900HV以上,處于世界頂尖水平。除此以外,采用該技術(shù)后軸承壽命和可靠性得到大幅度提高,平均壽命達(dá)到計算壽命的26倍,可靠性達(dá)99.9%。更令人驚喜的是,本技術(shù)可以顯著提高材料利用率,且生產(chǎn)流程可縮短2/3,真正在綠色發(fā)展上見實效。通過這項技術(shù)改性后的軸承鋼已在多個項目中得到運用,完全能夠滿足高端質(zhì)量要求,將該技術(shù)運用到其他材料中,也取得了非常良好的效果,運用于鈦合金和高溫合金中屬于世界首創(chuàng)。
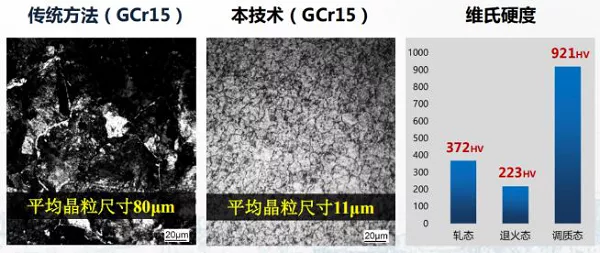
圖2 較于傳統(tǒng)技術(shù),PTR技術(shù)單道次晶粒細(xì)化程度高[2]
另外,經(jīng)過長期的科研攻關(guān),劉東教授團(tuán)隊還先后突破近10項關(guān)鍵技術(shù),極大地提升了航空發(fā)動機(jī)性能,讓著顆現(xiàn)代工業(yè)皇冠上的明珠更亮、更耀眼。出于保密原因,這些關(guān)鍵技術(shù)叫什么名字,通過哪些工藝實現(xiàn),筆者在這里不得而知。唯一知曉的是在2020年1月,因為這項貢獻(xiàn),團(tuán)隊負(fù)責(zé)人劉東教授在人民大會堂,從國家領(lǐng)導(dǎo)人手中,接過國家級獲獎證書。
4)由西南鋁牽頭研究開發(fā)的5m級鋁合金異形環(huán)試制取得重大突破;
鋁合金在生活中非常常見,同時高質(zhì)量的鋁合金在航空航天等工業(yè)有著非常重要的應(yīng)用。到目前為止,鋁合金的大規(guī)格棒材,板材均已經(jīng)成熟,但是大規(guī)格鋁合金異形環(huán)件在國內(nèi)研究尚為空白。大規(guī)格環(huán)材在航天事業(yè)上可謂要求迫切。但要突破這項技術(shù),需從鍛造開坯、異形環(huán)軋制、熱處理方面開展系統(tǒng)的研究工作,技術(shù)難度非常大。現(xiàn)階段的工業(yè)中大型環(huán)件多為矩形環(huán)件,厚度大,穩(wěn)定性差,不能滿足高性能輕質(zhì)火箭要求,而一體成型的異形環(huán)件,材料利用率高,且在性能和流線上都具有較大優(yōu)勢。為此,西南鋁通過仿真模擬輔助軋制成形技術(shù),設(shè)計出了6種坯料的形狀尺寸、模具,在建立環(huán)件軋制仿真過程中,應(yīng)用單一變量原則對驅(qū)動輥轉(zhuǎn)速、芯輥進(jìn)給速度、抱輥運動曲線等參數(shù)進(jìn)行優(yōu)化設(shè)計,制定合理的生產(chǎn)工藝。經(jīng)過3年的反復(fù)攻關(guān),西南鋁根據(jù)試制結(jié)果不斷調(diào)整優(yōu)化方案,解決了異形環(huán)件在生產(chǎn)過程中產(chǎn)生振動、爬輥等問題,獲得了成形效果良好、性能穩(wěn)定的環(huán)件,為后續(xù)生產(chǎn)奠定基礎(chǔ)。此異形環(huán)件為某重點型號工程用關(guān)鍵構(gòu)件--貯箱過渡環(huán)。相比傳統(tǒng)矩形環(huán)件,此異形環(huán)件投料節(jié)省40%左右,大大減小投料鑄錠直徑,增大變形程度和提高熱處理效果。
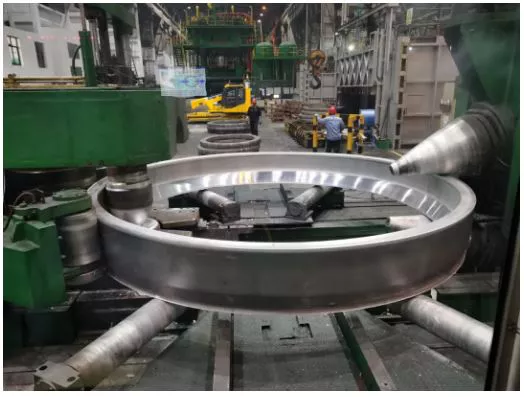
圖3 西南鋁牽頭研究開發(fā)的5m級鋁合金異形環(huán)[3]
5)金屬所鈦合金團(tuán)隊在“奮斗號”萬米全海深鈦合金取得突破;
全海深載人潛水器是難度極高的工程裝備,尤其是在潛入海深10000米時,材料將受到巨大的水壓,這就要求其具有非常高的強(qiáng)度,另外為了成型,材料還必須要有良好的塑性。另外,材料的焊接性必須良好,且焊接后的焊縫必須要具有良好的性能。要開發(fā)出這樣綜合性能優(yōu)異的材料,對材料專家來說,挑戰(zhàn)難度非常大。由金屬所牽頭,聯(lián)合寶鈦股份有限公司和中國船舶集團(tuán)公司洛陽船舶材料研究所,發(fā)揮三家單位的技術(shù)優(yōu)勢,組建了全海深鈦合金載人艙研制國家隊,開發(fā)并集成應(yīng)用了多項鈦合金材料技術(shù)和焊接加工技術(shù),攻克了一系列關(guān)鍵技術(shù)瓶頸,填補(bǔ)了多項國、國際技術(shù)空白,整體達(dá)到了國際領(lǐng)先地位水平,揭開了深海材料的劃時代意義。其研制Ti62A鈦合金,其韌性和可焊性與Ti64相當(dāng),強(qiáng)度提高20%。成功解決了載人艙材料所面臨的強(qiáng)度、韌性和可焊性等難題。
6)潘錦功成功研發(fā)碲化鎘太陽能發(fā)電玻璃,發(fā)明34項自主專利
說起錢學(xué)森,在科技界恐怕無人不知,無人不曉。他為我國的兩彈一星事業(yè)做出了極大地貢獻(xiàn),具體涉及到航天、導(dǎo)彈以及火箭。可以說,他的回歸,直接讓中國的航天事業(yè)提前推進(jìn)20年。對于這樣一位愛國的科學(xué)家,筆者心里由衷的敬佩。其實中國又出了一個“錢學(xué)森”,他就是“發(fā)電玻璃”的創(chuàng)始人潘錦功。
煤、石油為不可再生資源,隨著社會的發(fā)展,他們的儲備早已入不敷出,逐漸枯竭,尋找可再生能源已是迫在眉睫。太陽能是一種取之不竭,用之不盡的能源,是目前為止最為安全、高校以及環(huán)保的資源,超越了風(fēng)能和核能。目前所用的太陽能電池板價格高昂,而且轉(zhuǎn)化率也不高。
在潘錦功博士及其團(tuán)隊的努力下,2017年他們制作出具有中國完全自主知識產(chǎn)權(quán)的“發(fā)電玻璃”。這項技術(shù)領(lǐng)先國際,可以為未來的能源問題提供一條坦途。可以毫不夸張地說,這項發(fā)明足以改變世界。這種發(fā)電玻璃制備工藝簡單,只需要在普通普通玻璃上,均勻涂抹4微米厚的碲化鎘光電薄膜。而且生產(chǎn)一塊面積1.9平方米的發(fā)電玻璃,只需要55秒。它可以用于可導(dǎo)電,可發(fā)電的半導(dǎo)體材料。同時,這塊玻璃的光電轉(zhuǎn)化率達(dá)到17.8%,足以媲美傳統(tǒng)太陽能板。1.92平方米的“發(fā)電玻璃”,每年產(chǎn)生260度到270度的電,只需兩三塊就能供一個家庭的全年用電,三四千塊玻璃的發(fā)電量堪比一口普通油田一年產(chǎn)油所轉(zhuǎn)化的電量。
現(xiàn)代的城市生活可謂是燈紅酒綠,各種商業(yè)活動,居民用電等嚴(yán)重消耗著世界的能源。如果將建筑物中的玻璃,全部改為發(fā)電玻璃,就可以大大節(jié)煤炭發(fā)電廠的能源,而且很方便的給用戶提供電力保障。有人統(tǒng)計過,中國將近有400多億平方米的建筑,如果全部改為發(fā)電玻璃,其發(fā)電量相當(dāng)于建設(shè)30個三峽水電站。如此一來,每年將節(jié)約的資源堪稱天文數(shù)字,除了用在建筑上之外,這種玻璃還能用于軍事。在野外,只需要帶上一小塊玻璃,就能夠保障軍區(qū)通訊基站的用電需求。它甚至還能被鋪在路面上,如果用于電動汽車,那么這樣的路面可以別隨時用作移動充電站。甚至于將汽車玻璃改造成“發(fā)電玻璃”。能夠直接為汽車提供能源。看完這些,大家恐怕就知道這款發(fā)電玻璃有多魔性了吧。
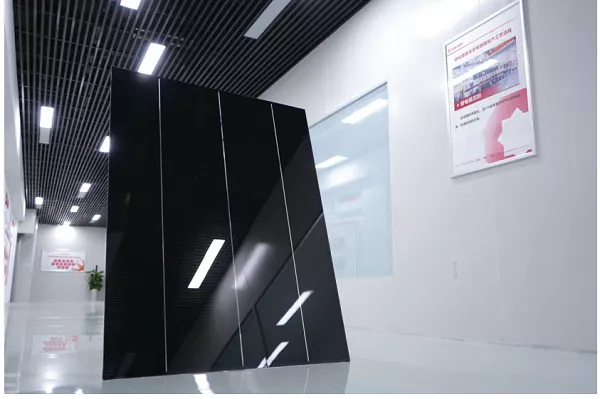
圖4 普通發(fā)電玻璃展示 [4]
參考文獻(xiàn):
[1] Mingyue Sun, Bin Xu, Bijun Xie, Dianzhong Li, Yiyi Li. Leading manufacture of the large-scale weldless stainless steel forging ring: Innovative approach by the multilayer hot-compression bonding technology. Journal of Materials Science & Technology 71 (2021) 84–86.
[2] 西北工業(yè)大學(xué)公眾號,2021.03.31
[3] 中鋁西南鋁業(yè)官網(wǎng)。
[4] 葉濤,周書婷, 四川省創(chuàng)新專家、 成都中建材光電材料有限公司總經(jīng)理潘錦功:用材料革命推動產(chǎn)業(yè)革命。《產(chǎn)城》,2019.
免責(zé)聲明:本網(wǎng)站所轉(zhuǎn)載的文字、圖片與視頻資料版權(quán)歸原創(chuàng)作者所有,如果涉及侵權(quán),請第一時間聯(lián)系本網(wǎng)刪除。
相關(guān)文章
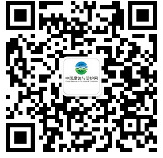
官方微信
《中國腐蝕與防護(hù)網(wǎng)電子期刊》征訂啟事
- 投稿聯(lián)系:編輯部
- 電話:010-62316606-806
- 郵箱:fsfhzy666@163.com
- 中國腐蝕與防護(hù)網(wǎng)官方QQ群:140808414
文章推薦
點擊排行
PPT新聞
“海洋金屬”——鈦合金在艦船的
點擊數(shù):7130
腐蝕與“海上絲綢之路”
點擊數(shù):5741