一 案例背景
化工生產中的載體焙燒爐是生產過程中的關鍵設備,其爐筒在長時間高溫、強腐蝕性介質的環境下運行,容易受到腐蝕損傷,最終導致爐筒斷裂,影響生產安全。本案例將分析一起化工生產高溫焙燒爐腐蝕減薄失效導致爐筒斷裂的事故。
二
案例經過
某企業載體焙燒單元使用回轉式高溫焙燒爐,爐筒周長約6米,長度約20米。爐筒材質為日本進口的INCONEL 600鎳基高溫合金焊接而成,爐內抄料板材質為310S超級奧氏體不銹鋼。焙燒爐工藝溫度約為700~900℃。生產工況環境涉及氧化鋁、硫(硫酸根、硫離子、二氧化硫)、磷酸根(偶爾)、硝酸(助劑)和水蒸汽等。在高溫酸性硫環境下設備運行12個月,預焙燒段爐筒筒節離進料端1~1.5米處(長度約3米)腐蝕減薄嚴重,抄料板沿焊縫腐蝕開裂并頻繁掉落。在設備運行18個月時,預焙燒段爐筒筒節發生本體脆裂,筒節外壁可見之字形裂紋,見下圖所示。該事故導致非計劃停工,僅更換爐筒段一次直接費用就三百多萬元,考慮到爐筒斷裂導致停產的間接損失更是不可設想。
三
高溫硫腐蝕主要發生在焙燒爐筒的內部,當硫化物在高溫下與爐筒材料(如不銹鋼、合金鋼等)接觸時,會發生化學反應,生成硫化物膜。這種膜在應力作用下容易破裂,導致腐蝕介質直接接觸到新鮮的金屬表面,從而加速了腐蝕過程。隨著時間的推移,爐筒壁厚會逐漸減薄,嚴重影響其結構完整性和使用壽命。
02
高溫焙燒爐內部存在高溫煙氣,這些煙氣中含有大量的腐蝕性物質,如氧氣、氮氧化物、硫氧化、磷氧化物等。在高溫條件下,這些腐蝕性物質與爐筒金屬壁面發生復雜的物理化學反應,導致爐筒表面逐漸被腐蝕。
高溫條件下物料中存在的酸性介質,特別硫(硫酸根、硫離子、二氧化硫)、磷酸、硝酸等腐蝕性介質。對于某些不銹鋼材料,雖然在一定溫度下具有一定的耐腐蝕性,但在長期高溫酸性條件下仍可能發生嚴重的腐蝕,腐蝕速率隨溫度上升而顯著增加。
煙氣中的微量水蒸氣與H2S結合生成酸,當爐筒表面的溫度低于露點溫度時,H2S的飽和蒸汽會凝聚成液體并吸附于爐筒表面,導致爐筒表面嚴重腐蝕。
載體焙燒過程中,硫化物的存在無法避免。當硫化物在高溫高應力環境下與爐體材料接觸時,就可能引發應力腐蝕。這種腐蝕通常發生在爐體的焊縫位置以及各部件的連接處,譬如材質為310S抄料板的焊縫。
選擇更耐腐蝕的材料,如Inconel 625合金材料、哈氏合金C276材料、鈦合金材料等。材料升級必然會帶來企業設備成本顯著增加,需綜合考慮材質升級的性價比。
通過選擇合適的焊條和焊接工藝優化,可以減少焊縫發生應力腐蝕開裂的幾率。選用合適焊條并嚴格控制焊接電流和焊接速度;首道焊接氬弧焊打底,每道約3mm厚;焊接溫度不要超過100℃,盡量減少焊接應力集中及焊縫材質發生改變。
采用無機陶瓷涂料層或高性能耐蝕陶瓷合金復合涂層對爐筒表面進行防腐處理,降低露點腐蝕的速度。
通過控制焙燒過程中的溫度和氣氛,減少硫化物的生成和積聚,從而降低應力腐蝕的風險。
通過加強煙氣管理,降低煙氣中腐蝕性物質,如氧氣、氮氧化物、硫氧化、磷氧化物等的含量,減少煙氣在預焙燒段的停留時間,從而減輕露點腐蝕和高溫煙氣腐蝕。
定期對爐筒的腐蝕情況進行監測和評估,通過人工檢測、超聲測厚等手段,及時發現和處理潛在的腐蝕問題。
化工生產過程中載體焙燒爐的腐蝕失效是一個復雜的過程,涉及多種腐蝕機理的共同作用。通過選擇更耐腐蝕的材料、加強焊后熱處理、表面防腐處理、加強工藝管理和煙氣管理、定期監測與評估、加強設備的維護和檢修等措施,可以有效預防和減少爐筒腐蝕失效的發生,確保化工生產生產裝置的安全穩定運行。
免責聲明:本網站所轉載的文字、圖片與視頻資料版權歸原創作者所有,如果涉及侵權,請第一時間聯系本網刪除。
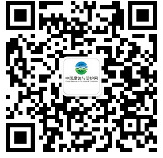
官方微信
《腐蝕與防護網電子期刊》征訂啟事
- 投稿聯系:編輯部
- 電話:010-62316606
- 郵箱:fsfhzy666@163.com
- 腐蝕與防護網官方QQ群:140808414