CO2地質(zhì)利用與封存環(huán)境下鋼材腐蝕行為與腐蝕控制措施研究進展
2024-03-05 16:48:08
作者:腐蝕與防護 來源:腐蝕與防護
分享至:
隨著全球工業(yè)的不斷發(fā)展,大量以CO2為代表的溫室氣體被排入大氣中,地球正經(jīng)歷日益嚴(yán)重的氣候變暖過程。聯(lián)合國政府間氣候變化專門委員會(IPCC)在2021年度報告中指出:截至2019年,CO2的年平均質(zhì)量濃度已達到410 mg/L,大氣CO2濃度已達到200萬年以來最大值;若不加以控制,將對自然生態(tài)系統(tǒng)和人類生活環(huán)境造成巨大威脅。CO2地質(zhì)利用與封存(CGUS)技術(shù)是目前較為有效的CO2減排方式,其主要是通過工程技術(shù)手段將捕集的CO2注入地下,利用地質(zhì)條件生產(chǎn)或強化能源、資源開采,同時實現(xiàn)注入CO2與大氣長期隔絕的過程。在CGUS過程中,鋼材腐蝕可能發(fā)生在CO2輸送、驅(qū)油利用、咸水層封存等多個過程中,主要的腐蝕方式有金屬管道腐蝕、井筒油管和套管腐蝕、設(shè)備閥門與井筒閥門腐蝕等,如圖1所示。
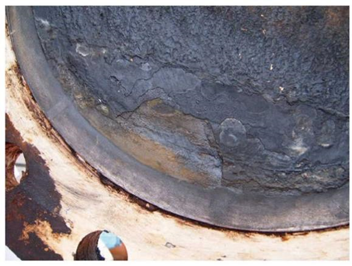
我國已有部分試驗性和驅(qū)油用管道投入運行,在勝利油田、鄂爾多斯盆地、準(zhǔn)噶爾盆地等地開展了規(guī)模化CGUS項目建設(shè)。為最大限度地減少CO2腐蝕導(dǎo)致的安全風(fēng)險,開展CO2地質(zhì)利用與封存環(huán)境下鋼材腐蝕行為研究十分必要。
干燥的CO2本身并沒有腐蝕性,但在儲存、輸送和利用過程中,不可避免地會接觸水和其他雜質(zhì)。當(dāng)CO2溶于水后,其酸度往往比相同pH的鹽酸更高,對鋼材的腐蝕更嚴(yán)重。
相比于一般井下CO2腐蝕環(huán)境,為了提高CO2封存效率,CGUS過程一般向地下注入大量超臨界態(tài)CO2,會在含水層中形成獨立的超臨界CO2相,并具有很高的分壓(超臨界CO2相分壓一般在10 MPa以上)。在此條件下,CO2在水中的溶解度顯著增加,形成具有強腐蝕性的碳酸溶液,極端條件下碳酸溶液的pH值可降至3以下,極大地增加了井下管柱發(fā)生腐蝕的風(fēng)險,從而更容易導(dǎo)致泄漏等安全事故的發(fā)生。
考慮到CGUS技術(shù)的應(yīng)用現(xiàn)狀和發(fā)展前景,探明CGUS環(huán)境下的鋼材腐蝕行為及機理,明確CO2腐蝕的影響因素,探究相應(yīng)的防腐措施,對揭示鋼材CO2腐蝕規(guī)律、規(guī)避CO2腐蝕風(fēng)險、實現(xiàn)CO2減排,具有十分重要的現(xiàn)實意義。
CO2腐蝕鋼材總的反應(yīng)并不復(fù)雜,生成的腐蝕產(chǎn)物主要為FeCO3,其在一定條件下對鋼材表面能夠起到保護作用。溶解于水中的CO2會改變水溶液的化學(xué)性質(zhì),形成的H+、HCO3–、CO32–等離子會影響鋼材腐蝕的電化學(xué)反應(yīng)(包括陰極和陽極反應(yīng))。與單純的強酸腐蝕和氧化腐蝕相比,CO2作用下鋼材腐蝕的陰極和陽極反應(yīng)過程更為復(fù)雜。
在CO2水環(huán)境下,陰極反應(yīng)機制會受到溶液條件的影響。針對碳酸鹽離子對陰極反應(yīng)的影響,有直接還原和“緩沖效應(yīng)”兩種不同的反應(yīng)機制。這兩種機制并不相互排斥,但理清更適用于解釋CO2對腐蝕影響的機制至關(guān)重要。
“緩沖效應(yīng)”機制僅考慮H+的還原,H2CO3和HCO3–只是作為貯存H+的“容器”,隨著H+的還原而減少,反應(yīng)式如下:
而在直接還原機制中,H2CO3和HCO3–中的H+可能直接被還原,反應(yīng)式如下:
Remita等使用電化學(xué)技術(shù)研究了與HCO3–離子相關(guān)的“緩沖效應(yīng)”機制。他們開發(fā)了一個僅考慮H+還原和“緩沖效應(yīng)”的模型,并利用該模型擬合了在不同轉(zhuǎn)速、飽和與非飽和CO2溶液條件下的極化曲線,用于解釋在飽和CO2溶液中測得較高極限電流的原因,從而證明了“緩沖效應(yīng)”機制的合理性。
Kahyarian等使用了類似的方法來證實“緩沖效應(yīng)”機制,他們的模型認為H+還原是唯一可能發(fā)生的陰極反應(yīng),其通量方程綜合了腐蝕溶液中所有酸和堿的均相反應(yīng)速率,能夠預(yù)測CO2飽和溶液的動電位陰極極化(圖2),從而得到鋼材電化學(xué)腐蝕過程的動力學(xué)特征,包括腐蝕速率的確定、腐蝕控制因素的分析、腐蝕機理等。
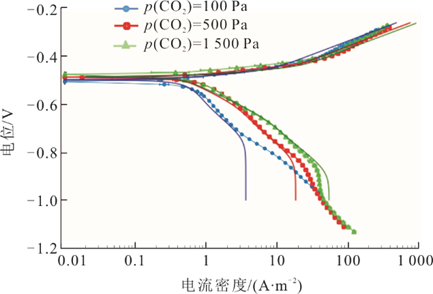
圖2 API 5L X65低碳鋼在10 ℃、0.1 mol/L NaCl溶液、 4.6 m/s流速、pH=6以及p(CO2)=100、500、1500 Pa條件下的極化曲線(實線為模型預(yù)測曲線)
直接還原機制通常用于解釋在水溶液中CO2溶解量較大、濃度較高時具有較高腐蝕速率的現(xiàn)象。Nesic等人在另一項研究中指出,在含有CO2的水溶液中,腐蝕極限電流高于在相同pH值的HCl溶液中的腐蝕極限電流。他們將這種現(xiàn)象歸因于金屬表面上H2CO3的直接還原。
Gulbransen和Bilkova通過線性極化電阻(LPR)和失重法測量也發(fā)現(xiàn),隨著溶液中乙酸濃度的增加,即使陽極反應(yīng)(Fe發(fā)生溶解)受到抑制,腐蝕速率依然會增加。他們也將這種現(xiàn)象歸因于碳酸和乙酸的直接還原。
與陰極反應(yīng)類似,陽極反應(yīng)同樣受到溶液條件的影響。在CO2存在的情況下,F(xiàn)e溶解的陽極反應(yīng)途徑依然存在爭議,特別是CO2在金屬表面或其他中間產(chǎn)物表面上的吸附機制尚未完全闡明。確定陽極反應(yīng)機制是預(yù)測腐蝕過程動力學(xué)的關(guān)鍵。Heusler和Bockris使用電化學(xué)技術(shù)研究了陽極反應(yīng)過程,提出了催化機制(Heusler機制)和連續(xù)機制(Bockris機制)兩種不同的機制。在催化機制中,生成的中間產(chǎn)物FeOHads與催化劑類似,能夠加快Fe溶解的進程且自身沒有發(fā)生變化,反應(yīng)式如下:
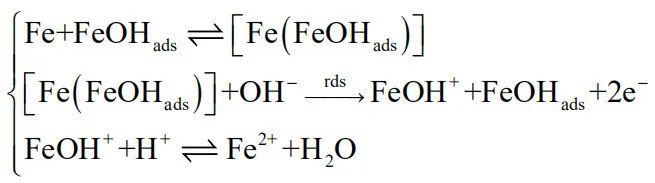
而在連續(xù)機制中,F(xiàn)e的溶解被認為是一種連續(xù)的“序列”,中間產(chǎn)物FeOHads隨著反應(yīng)的進行會發(fā)生不可逆的變化,反應(yīng)式如下:
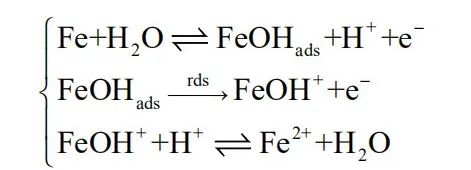
Kahyrian等同樣研究了在不同CO2分壓下CO2對陽極反應(yīng)的作用,發(fā)現(xiàn)在不同CO2分壓下測得的塔菲爾斜率系數(shù)略有不同。這證明了CO2參與了陽極反應(yīng)。
溶解在水中的“碳”對電化學(xué)反應(yīng)有重大影響。在pH值相同的情況下,由于直接還原或“緩沖效應(yīng)”機制,CO2的存在會增加腐蝕速率。CO2分壓越高,腐蝕電流越大。由于中間產(chǎn)物的復(fù)雜性和多樣性,CO2在陽極反應(yīng)中的作用尚未完全了解。目前來說,仍然需要利用電化學(xué)技術(shù)對CO2腐蝕鋼材的陰極和陽極反應(yīng)機制加以深入研究。
CGUS過程所面臨的地層條件十分復(fù)雜,特別是在CO2注入后,會將環(huán)境改變?yōu)楦逤O2濃度、低pH的腐蝕性環(huán)境。與此同時,地層下的高溫高壓條件、雜質(zhì)離子及氣體、液體的流動沖刷等各項因素相互作用,將會影響甚至改變鋼材的腐蝕過程。
CO2分壓對鋼材的腐蝕具有顯著的影響,隨著井下壓力不斷發(fā)生變化,CO2的相態(tài)也將發(fā)生相應(yīng)的改變。在不同的相態(tài)下,鋼材的腐蝕情況也有所不同。吳保玉等研究了在非臨界、亞臨界、超臨界(6、7、8、10 MPa)3種工況下CO2/H2O體系中N80鋼和J55鋼的腐蝕行為。結(jié)果表明在超臨界環(huán)境下,N80鋼和J55鋼的腐蝕速率均高于非臨界環(huán)境,并且在超臨界CO2/H2O體系CO2相和H2O相中,鋼材的腐蝕類型不同。H2O相中,鋼材以相對均勻的全面腐蝕為主;而CO2相中,鋼材則表現(xiàn)為顯著的局部坑蝕(圖3)。壓力不僅影響相態(tài)的改變,還會影響腐蝕產(chǎn)物的形成過程,并通過影響CO2的溶解度導(dǎo)致體系中H2CO3等物質(zhì)的含量以及pH值發(fā)生變化,進而影響整個腐蝕過程。CO2在水中的溶解度隨CO2分壓的增加而顯著增加。在大氣壓條件下,CO2在純水中的溶解度僅為0.029 mol/kg(0.1 MPa,30 ℃);而在CGUS條件下,CO2分壓可達10 MPa以上,對應(yīng)的溶解度達到了1.361 mol/kg(10 MPa,30 ℃)。
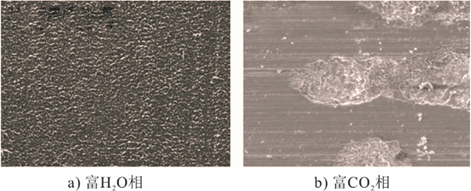
圖3 超臨界CO2/H2O體系在富H2O相和富CO2相環(huán)境下N80鋼微觀腐蝕形貌
CO2分壓的變化會影響水與CO2的互溶度,從而改變腐蝕性物質(zhì)的濃度,進而影響腐蝕過程。在相同的溫度下,鋼材在超臨界CO2環(huán)境中的腐蝕速率要遠遠大于低壓氣態(tài)環(huán)境。這是因為在超臨界狀態(tài)下,CO2在水中的溶解度會迅速增大,造成超臨界狀態(tài)下水溶液中H2CO3、HCO3–、CO32–等腐蝕性介質(zhì)的濃度增大,相應(yīng)的陰極反應(yīng)速率加快,最終加快腐蝕速率。與CO2在水中溶解度增大類似,在低壓氣態(tài)環(huán)境中,水在CO2中的溶解度遠大于超臨界環(huán)境。
Wei等計算出1 MPa時水在CO2中的溶解度約為10 MPa時的4倍,這說明低壓時有較多的水分溶解于CO2中,只有少量水分凝結(jié)析出;而超臨界環(huán)境下恰恰相反,大量的水凝結(jié)在鋼材表面,其中的腐蝕性物質(zhì)濃度遠高于低壓環(huán)境,因此腐蝕程度更嚴(yán)重。
相關(guān)研究表明,溫度會改變鋼材表面腐蝕產(chǎn)物膜的結(jié)構(gòu),進而影響腐蝕速率。在CGUS過程中,井下管柱的埋藏深度通常超過800 m,溫度隨著埋藏深度的增大可從常溫升高至100 ℃左右,因此對該溫度范圍內(nèi)鋼材CO2腐蝕行為開展研究是發(fā)展CGUS技術(shù)的重要內(nèi)容。李大朋等通過試驗發(fā)現(xiàn):在CO2分壓4 MPa的條件下,溫度較低時,N80鋼的腐蝕產(chǎn)物晶粒粗大,堆垛較疏松,保護性較差;溫度升高后,腐蝕產(chǎn)物膜更致密,腐蝕速率降低。張均生等也研究了不同溫度對平均腐蝕速率和點蝕速率的影響。結(jié)果表明在30 ℃時,平均腐蝕速率與點蝕速率均處于較低水平;而隨著溫度的升高,平均腐蝕速率于60 ℃達到最大值,點蝕速率于90 ℃達到最大值;溫度繼續(xù)升高至120 ℃,腐蝕產(chǎn)物膜與基體間結(jié)合更加緊密,保護作用增強,腐蝕速率下降。李黨國等利用交流阻抗技術(shù)研究了在模擬地層水中溫度對鋼材CO2腐蝕的影響。他們觀察到:低溫下出現(xiàn)了與雙電層電容和傳遞電阻有關(guān)的高頻容抗弧,對應(yīng)于腐蝕產(chǎn)物膜活性溶解的中低頻感抗弧和與腐蝕產(chǎn)物膜生成有關(guān)的低頻容抗弧3個時間常數(shù);隨著溫度的升高,感抗弧逐漸縮小直至消失,而低頻容抗弧則逐漸擴大,有利于腐蝕產(chǎn)物膜的生成;傳遞電阻也逐漸增大,說明腐蝕產(chǎn)物膜的致密性增強,從而更好地保護基體,減小腐蝕速率。
就目前而言,針對CGUS環(huán)境中溫度變化對CO2狀態(tài)的改變、CO2與水的互溶度、鋼材表面腐蝕機理等方面的研究并不多見,依然需要開展針對性的試驗進行探究。
流速的變化會改變鋼材表面腐蝕產(chǎn)物膜的結(jié)構(gòu)性能,如致密程度、對鋼材的保護作用等。高純良等研究了流速對N80鋼CO2腐蝕行為的影響,結(jié)果表明隨著流速的增大,腐蝕產(chǎn)物膜的破壞加劇,保護性降低,腐蝕速率幾乎呈指數(shù)形式增長。
李巖巖等發(fā)現(xiàn),在超臨界CO2環(huán)境中,流體流動加速了腐蝕性物質(zhì)向鋼材表面?zhèn)髻|(zhì)過程,同時對鋼材表面施加了剪切應(yīng)力,破壞了FeCO3膜的完整性和致密性(圖4),從而加快了腐蝕速率。除此之外,流速變化還可能造成鋼材的局部腐蝕。
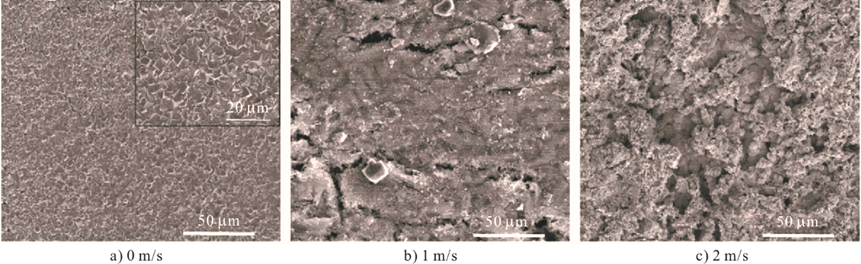
圖4 N80鋼在60 ℃、不同流速超臨界CO2地層水中腐蝕24 h后的表面形貌
Schmitt等研究發(fā)現(xiàn),當(dāng)流體的流動速度或強度達到一定程度時,就能夠抑制具有保護作用的腐蝕產(chǎn)物膜的再生,而局部腐蝕就會在腐蝕產(chǎn)物膜剝落的部位發(fā)生。
雖然目前已經(jīng)明確了流速對鋼材腐蝕會產(chǎn)生一定的影響,但針對高濃度CO2環(huán)境,特別是在環(huán)境條件十分復(fù)雜的地層作用下多相流對鋼材腐蝕造成影響的研究并不多見,因此仍然需要進行大量的實驗研究以探明在CGUS環(huán)境中流體流動條件下鋼材的腐蝕行為及腐蝕機理。
隨著石油和天然氣需求量的不斷增大,越來越多的非常規(guī)油氣田被勘探和開采,由于這類油氣田的礦化度較高,腐蝕性較強,CGUS應(yīng)用風(fēng)險也隨之增大。目前的研究主要關(guān)注高礦化度采出水對鋼材CO2腐蝕的影響。Dong等研究發(fā)現(xiàn),隨著礦化度的增加,X60鋼腐蝕產(chǎn)物的形態(tài)和密度發(fā)生了改變,鋼的表面腐蝕產(chǎn)物由松散變?yōu)橹旅埽Wo性增強。薛玉娜等采用電化學(xué)方法研究了CT80鋼在高礦化度油井水中的腐蝕行為以及礦化度對腐蝕過程的影響。結(jié)果表明,隨著礦化度的增大,CT80鋼的開路電位正移,電荷傳遞電阻先減小后增大,在電阻最小時出現(xiàn)腐蝕速率最大值。出現(xiàn)這種結(jié)果,可能與溶液中的溶解氧有關(guān)。溶液的pH值是影響鋼制管材腐蝕的重要因素。Wang等發(fā)現(xiàn),隨著pH值從6降至2,碳鋼的腐蝕速率增加了近10倍。Pessu等研究了pH值對X65鋼在CO2飽和鹽水中點蝕行為的影響。結(jié)果表明,隨著pH值的增大,X65鋼表面的腐蝕產(chǎn)物由無保護性的Fe3C逐漸演變?yōu)榫哂斜Wo作用的FeCO3,總的腐蝕速率也隨之降低。
Deng等采用電化學(xué)方法研究了不同pH值對X80鋼沖蝕行為的影響,發(fā)現(xiàn)隨著pH值的增加,X80鋼的自腐蝕電位負移,腐蝕電流密度呈逐漸減小的趨勢,阻抗譜圖的電容和電阻弧半徑逐漸增大,總極化電阻增大,腐蝕速率降低,耐蝕性提高(圖5)。
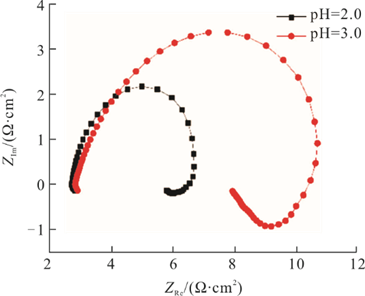
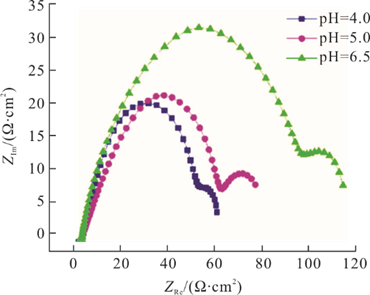
圖5 X80鋼在不同pH值下阻抗譜圖
以上研究結(jié)果表明:在單一條件下,隨著礦化度的增大,鋼材的腐蝕速率隨之加快;隨著pH的增大,鋼材的腐蝕速率隨之減慢。但在多相條件下,兩者對鋼材CO2腐蝕的影響程度和影響規(guī)律依然沒有達成統(tǒng)一的認識,還需要進一步的探究。
在CGUS過程中,想要得到單一的CO2環(huán)境是幾乎不可能做到的。地層中往往含有一定量的水和腐蝕性雜質(zhì)(如O2、SO2、H2S、NO2),這些雜質(zhì)與H2O、CO2共同作用,對鋼材造成更為嚴(yán)重的腐蝕。O2作為一種強氧化劑,它的存在(特別是當(dāng)O2與CO2在水中共存時)會對鋼材受CO2腐蝕產(chǎn)生影響。黃天杰等發(fā)現(xiàn):當(dāng)CO2/O2體系中CO2分壓大于O2分壓時,N80鋼的腐蝕以CO2腐蝕為主,腐蝕產(chǎn)物膜的成分主要為FeCO3,產(chǎn)物膜呈晶態(tài)結(jié)構(gòu),具有較好的保護作用;而當(dāng)O2分壓較大時,則是以O(shè)2腐蝕為主,腐蝕產(chǎn)物膜的成分以Fe的氧化物為主,F(xiàn)eCO3只占少部分,產(chǎn)物膜疏松,幾乎沒有保護作用。孫永濤等的研究也得到了類似的結(jié)果:當(dāng)CO2/O2體系中O2為微量時,起主導(dǎo)作用的是CO2腐蝕過程,CO2參與反應(yīng)形成的FeCO3具有保護作用;而體系中存在O2時,生成的FeOOH或Fe2O3不具有保護作用。H2S通常來源于天然氣生產(chǎn)及燃燒過程,是CGUS中常見的雜質(zhì)成分。與CO2/O2相比,CO2/H2S體系中的腐蝕行為更為復(fù)雜。學(xué)者們認為在CO2/H2S體系中,CO2對腐蝕具有促進作用,隨著其相對含量的增加,腐蝕過程將逐步轉(zhuǎn)化為由CO2主導(dǎo)。而H2S既可以直接參與陰極反應(yīng),加劇CO2腐蝕;也可與Fe反應(yīng)生成FeS膜,減緩腐蝕。因此在CO2和H2S共存的環(huán)境中,兩者具有競爭或協(xié)同效應(yīng)。目前針對CO2/H2S的研究,主要是從分壓比這一因素切入,但現(xiàn)有的研究對兩者主導(dǎo)腐蝕的分壓比界限劃分還沒有統(tǒng)一的標(biāo)準(zhǔn)。Sridhar等認為:CO2/H2S的分壓比大于200時(CO2主導(dǎo)腐蝕),CO2是主要的腐蝕介質(zhì),腐蝕速率與鋼材表面生成的FeCO3膜的結(jié)構(gòu)性能密切相關(guān);CO2/H2S的分壓比小于或等于200時(H2S主導(dǎo)腐蝕),H2S的存在會使鋼材表面優(yōu)先生成一層致密的FeS膜,從而阻礙FeCO3膜的生成,而這層FeS膜是否起保護作用則與溫度和酸堿度有關(guān)。對于分壓比界限的劃分,Pots等持有不同的觀點。他們認為當(dāng)CO2/H2S的分壓比小于20時,H2S控制腐蝕過程,腐蝕產(chǎn)物主要為FeS;當(dāng)分壓比處于20~500時,CO2與H2S混合交替控制腐蝕過程,腐蝕產(chǎn)物包含F(xiàn)eS和FeCO3;當(dāng)分壓比大于500時,CO2控制腐蝕過程,腐蝕產(chǎn)物主要為FeCO3。SO2同樣會對鋼材的腐蝕造成影響。其原因在于SO2與水反應(yīng)后生成H2SO3,從而降低了體系的pH值。當(dāng)上述體系中同時存在O2時,H2SO3進一步轉(zhuǎn)化為H2SO4,從而造成更嚴(yán)重的腐蝕問題。相關(guān)研究表明,當(dāng)O2、H2S、SO2、NO2這些腐蝕性雜質(zhì)共存時,可能會相互反應(yīng),形成新的腐蝕性物質(zhì)(如H2SO4、HNO3、S等),這些物質(zhì)的存在會影響鋼材的腐蝕進程。Barker等系統(tǒng)總結(jié)了各種雜質(zhì)之間可能發(fā)生的作用及鋼材在相應(yīng)環(huán)境中的腐蝕機制,指出除了在溶液-鋼材界面發(fā)生電化學(xué)腐蝕之外,O2、H2S、SO2、NO2之間還可以發(fā)生許多反應(yīng),但這些反應(yīng)對腐蝕產(chǎn)生的影響仍不明確,還有待于進一步研究。除了氣體之外,地層溶液中的一些離子同樣影響鋼材的腐蝕行為。當(dāng)溶液中存在Cl-時,鋼材的腐蝕速率會受到很大的影響。在通常情況下,Cl-會對鈍化膜造成破壞,容易導(dǎo)致點蝕的發(fā)生。Zhang等人通過電化學(xué)技術(shù)研究了J55鋼在NaCl/NaHCO3溶液中的點蝕行為,發(fā)現(xiàn)隨著Cl-的加入,腐蝕速率增加。Liu等研究發(fā)現(xiàn)隨著Cl-含量的增加,N80鋼的腐蝕速率先增大后減小。在達到最大值之前,Cl-含量的增加加快了陽極反應(yīng)速率,促進了腐蝕;而達到最大值后,Cl-含量的增加降低了CO2的溶解度,并對溶液中其他物質(zhì)參與腐蝕反應(yīng)產(chǎn)生影響,導(dǎo)致腐蝕速率降低。而當(dāng)溶液中存在Ca2+和Mg2+時,兩者可以降低CO2的溶解度,并產(chǎn)生CaCO3和MgCO3沉淀。由于CaCO3和MgCO3的晶體結(jié)構(gòu)與FeCO3相似,Ca2+和Mg2+能夠替代FeCO3結(jié)構(gòu)中的Fe2+,這可能導(dǎo)致腐蝕產(chǎn)物層結(jié)構(gòu)形態(tài)和保護性能的改變,從而影響CO2腐蝕鋼材的機制。緩蝕劑是一種以適當(dāng)?shù)臐舛群托问酱嬖谟诃h(huán)境中時,可以防止或減緩材料腐蝕的化合物或混合物。添加緩蝕劑是鋼材腐蝕防護中較為有效和廉價的方法,特別是在石油天然氣開采和運輸過程中得到了廣泛的應(yīng)用。針對CO2腐蝕環(huán)境,研發(fā)的緩蝕劑主要有咪唑啉類緩蝕劑、有機胺類緩蝕劑、季銨鹽類緩蝕劑3類。
目前,在能夠抑制CO2腐蝕的緩蝕劑中,咪唑啉及其衍生物的用量是最大的。其分子結(jié)構(gòu)主要包括含N的五元雜環(huán)(咪唑啉環(huán))、R1基團和R2基團(圖6)。趙景茂等研究了咪唑啉類緩蝕劑在CO2/H2S環(huán)境中的緩蝕效果,結(jié)果表明緩蝕效率可達86.8%。有機胺可以吸附在金屬表面,抑制Fe氧化菌的生長,抵抗CO2和微生物雙重腐蝕。
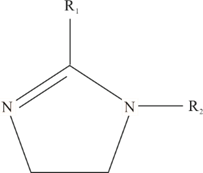
圖6 咪唑啉類緩蝕劑基本結(jié)構(gòu)
劉宏偉等研究了十二胺緩蝕劑對Q235鋼的緩蝕效果,發(fā)現(xiàn)在靜態(tài)條件下十二胺緩蝕劑的緩蝕效率可達93.44%;而在動態(tài)條件下,最低緩蝕效率也達到了87.93%,緩蝕效果較好。事實上,單組分緩蝕劑已經(jīng)難以滿足越來越苛刻的CO2腐蝕環(huán)境。因此,研究人員嘗試將緩蝕效果顯著的咪唑啉類緩蝕劑與其他緩蝕劑復(fù)配,從而得到緩蝕效果更好的緩蝕劑。咪唑啉季銨鹽具有比單組份咪唑啉更好的緩蝕性能,特別是在高溫高壓CO2/H2S環(huán)境下,可形成性能穩(wěn)定且不易分解的有機膜,具有較好的抗硫性能。Harris等研究了氯化二甲基芐基烴銨緩蝕劑對碳鋼CO2腐蝕的影響,結(jié)果表明緩蝕劑的緩蝕效果受溫度影響,在高溫條件下,緩蝕劑的加入會破壞碳鋼表面形成的FeCO3保護膜,造成緩蝕效率降低。因此,選擇應(yīng)用于高溫條件的緩蝕劑時,應(yīng)考慮其對腐蝕產(chǎn)物膜的影響,而關(guān)于這部分內(nèi)容的研究還較為少見。
盡管緩蝕劑的研究已經(jīng)取得了較多成果,但大多是在實驗室較為理想的CO2腐蝕環(huán)境得到的結(jié)果,實際CO2腐蝕環(huán)境十分復(fù)雜,緩蝕機理需進一步加強。能夠適應(yīng)大多數(shù)CO2腐蝕環(huán)境的緩蝕劑尚未面世,想要開發(fā)出綠色高效且適用范圍廣的緩蝕劑仍然需要不斷的探索。
涂層也是一種應(yīng)用廣泛的防腐措施。對于鋼材而言,有機涂層和金屬涂層具有優(yōu)異的屏障性能與陰極保護性能,可以保護其免受腐蝕的危害。賈營坤等將高溫?zé)徇€原氧化石墨烯(TRGO)作為二維納米填料添加到聚酰亞胺(PI)聚合物基質(zhì)中,制備出了TRGO/PI納米復(fù)合耐蝕涂層,其在海水中具有良好的腐蝕防護效果。蔣穹等制備出了熱燒結(jié)鋁鋅硅合金涂層,其具有陰極保護作用,并且Al-Zn-Si合金延緩了涂層金屬粉末的消耗,使?fàn)奚枠O的腐蝕速率減慢。管鐵鑫通過電化學(xué)技術(shù)測試了Fe基非晶涂層抗CO2腐蝕的能力,并與其他幾種金屬進行了比較,結(jié)果表明Fe基非晶涂層的抗CO2腐蝕能力顯著高于316L和Cr13等耐蝕金屬,具有優(yōu)異的耐蝕性能。王珂等測試了兩種涂層油管在油田CO2環(huán)境中耐蝕性能,結(jié)果表明與普通無涂層油管相比,內(nèi)涂層油管的腐蝕速率遠小于普通油管。
目前已經(jīng)研制出的涂層種類繁多,且均具有良好的防腐性能,然而涂層的現(xiàn)場應(yīng)用實例并不多見,原因可能在于涂層的制備成本較高,需要通過進一步的研究以降低其應(yīng)用成本。此外,針對CGUS環(huán)境中用于保護鋼材的防腐涂層研究還較為罕見,仍然需要通過大量實驗對防腐涂層的成分、防腐機理等進行探究。
在含有CO2的腐蝕環(huán)境下,選用耐蝕性好的鋼材往往能夠有效地延緩或阻礙腐蝕。相關(guān)研究表明,在鋼材中加入Cr元素能夠顯著提高其耐蝕性,且成本要低于同等級的傳統(tǒng)碳鋼。謝濤等對N80、L80、1Cr、3Cr、13Cr等5種不同材質(zhì)油套管鋼進行了CO2腐蝕試驗發(fā)現(xiàn),隨著Cr含量的增加,油套管鋼的腐蝕速率明顯降低。Muraki等觀察到Cr鋼在形成腐蝕產(chǎn)物膜之前,其瞬時腐蝕速率高于碳鋼,但隨后便顯著降低。他們認為發(fā)生這一現(xiàn)象的原因在于Cr鋼表面形成了具有保護作用的腐蝕產(chǎn)物膜,提高了Cr鋼的抗CO2腐蝕性能。Cr鋼表面腐蝕產(chǎn)物膜的主要成分為Cr(OH)3和Cr2O3,其中Cr(OH)3能夠阻礙FeCO3的形成,降低腐蝕產(chǎn)物膜中FeCO3的含量,使腐蝕產(chǎn)物膜變得致密,從而起到保護作用。大多數(shù)耐蝕合金,如鈦合金、316合金、鎳基合金等都含有Cr元素,并且每種耐蝕合金Cr元素含量及與其他合金元素含量的比例有所差異。這些合金在受到CO2腐蝕時,表面也會形成含有Cr元素的腐蝕產(chǎn)物層,并具有優(yōu)良的抗CO2腐蝕性能。呂祥鴻等研究發(fā)現(xiàn),TC4鈦合金在含CO2地層水中處于鈍化狀態(tài),隨著溫度的升高,其最大腐蝕速率僅為0.0012 mm/a。Firouzdor等研究了3種鎳基合金在超臨界CO2中的腐蝕行為,發(fā)現(xiàn)3種鎳基合金均表現(xiàn)出優(yōu)異的耐蝕性,并且三者的表面都有一層富Cr氧化物。綜上所述,耐蝕合金抗CO2腐蝕性能已經(jīng)得到證明,但對于Cr元素的添加量及其與其他合金元素含量的比例對鋼材耐蝕性能的影響程度還不夠明確,依然需要大量的實驗進行深入研究。此外,在面對高濃度CO2的苛刻腐蝕環(huán)境時,可以將耐蝕合金與緩蝕劑或涂層結(jié)合使用,從而得到更好的抗CO2腐蝕效果。然而,目前關(guān)于這方面的研究鮮有報道,還有待于深入研究。
總體而言,目前針對CGUS環(huán)境中的CO2腐蝕鋼材問題的研究仍然較少,在高濃度CO2腐蝕鋼材機理、各項環(huán)境因素影響CO2腐蝕機制、CO2腐蝕防護技術(shù)等方面的研究仍然存在一定的局限性。基于上述局限性,總結(jié)了CGUS環(huán)境中鋼材腐蝕方向的研究展望,具體包括:
(1) 當(dāng)前對CO2腐蝕鋼材的反應(yīng)機制依然存在爭議,特別是中間產(chǎn)物對陰極和陽極反應(yīng)過程的影響尚未厘清,需要通過大量的實驗進一步探究。(2) CO2腐蝕環(huán)境,特別是針對高濃度CO2多相流環(huán)境中的各項因素對CO2腐蝕的影響機制,以及它們共存時的協(xié)同作用和交互影響規(guī)律尚未完全闡明,需要大量的、系統(tǒng)的實驗加以研究。(3) CO2腐蝕防護技術(shù)仍存在應(yīng)用范圍窄、成本偏高的局限,緩蝕劑及涂層的應(yīng)用范圍具有一定的局限性。如想實現(xiàn)大規(guī)模的應(yīng)用,開發(fā)適用范圍廣、使用成本低、綠色高效的緩蝕劑將是今后研究的重點。此外,還需要對高壓高濃度CO2等更為苛刻條件下的緩蝕劑與涂層的研發(fā)開展更加深入的研究。耐蝕合金的研發(fā)還不夠充分,特別是對耐蝕合金中的耐蝕元素的含量及其對腐蝕程度的影響還需要繼續(xù)研究。
免責(zé)聲明:本網(wǎng)站所轉(zhuǎn)載的文字、圖片與視頻資料版權(quán)歸原創(chuàng)作者所有,如果涉及侵權(quán),請第一時間聯(lián)系本網(wǎng)刪除。