摘要
采用雙相區(qū)保溫+奧氏體化淬火+低溫退火的熱處理工藝, 研究了合金元素配分行為對C-Si-Mn系高強(qiáng)鋼微觀組織和力學(xué)性能的影響. 結(jié)果表明, 在760 ℃隨著保溫時間的延長, 雙相區(qū)中奧氏體相的體積分?jǐn)?shù)逐漸增多直至達(dá)到飽和, 而鐵素體向奧氏體擴(kuò)散的Mn元素含量也逐漸增多直至在兩相間達(dá)到化學(xué)勢平衡, 后加熱至930 ℃保溫120 s, 再淬火至220 ℃, 配分過程中發(fā)生了C從馬氏體向奧氏體中的擴(kuò)散偏聚. 經(jīng)該工藝處理后實驗用鋼的抗拉強(qiáng)度為1310 MPa, 延伸率可達(dá)12%, 強(qiáng)塑積達(dá)到15720 MPa.%, 相比傳統(tǒng)淬火+碳配分工藝, 雙相區(qū)保溫+奧氏體化淬火+低溫退火的熱處理工藝過程中Mn配分和C配分共同作用能夠顯著提高鋼中殘余奧氏體的含量和穩(wěn)定性, 從而提高高強(qiáng)鋼的室溫成形能力.
關(guān)鍵詞: 高強(qiáng)鋼 ; 雙相區(qū)保溫 ; Mn配分 ; C配分 ; 殘余奧氏體 ; 力學(xué)性能
本文引用格式
田亞強(qiáng), 張宏軍, 陳連生, 宋進(jìn)英, 徐勇, 張士宏. 低碳高強(qiáng)鋼合金元素配分行為對殘余奧氏體和力學(xué)性能的影響[J]. , 2014, 50(5): 531-539 https://doi.org/10.3724/SP.J.1037.2013.00709
TIAN Yaqiang, ZHANG Hongjun, CHEN Liansheng, SONG Jinying, XU Yong, ZHANG Shihong. EFFECT OF ALLOY ELEMENTS PARTITIONING BEHAVIOR ON RETAINED AUSTENITE AND MECHANICAL PROPERTY IN LOW CARBON HIGH STRENGTH STEEL[J]. 金屬學(xué)報, 2014, 50(5): 531-539 https://doi.org/10.3724/SP.J.1037.2013.00709
隨著汽車制造業(yè)發(fā)展以及鋼鐵冶金技術(shù)的不斷提升, 超輕型高強(qiáng)度汽車用鋼的開發(fā)與研究已歷經(jīng)了3個階段的發(fā)展. 從上世紀(jì)80年代末開始無間隙原子(IF)鋼的廣泛研究, 隨后發(fā)展了低合金高強(qiáng)度(HSLA)鋼、雙相(DP)鋼[1]、馬氏體(MART)鋼[2]、烘烤硬化(BH)鋼以及相變誘發(fā)塑性(TRIP)鋼[3-5]和孿晶誘發(fā)塑性(TWIP)鋼[6,7]. 其中, 合金元素對于高強(qiáng)鋼中的各種顯微組織和力學(xué)性能產(chǎn)生著重要影響. 合金元素在不同相中的平衡濃度并不一致, 可以改變相變溫度從而使鋼中各相的熱動力學(xué)穩(wěn)定性和相變動力發(fā)生變化, 促使相變或抑制相變, 并且影響鋼板顯微組織中各相的分布. 合金元素還通過固溶強(qiáng)化或析出強(qiáng)化的作用來提高強(qiáng)度并且影響晶粒尺寸, 最終影響鋼材的力學(xué)性能[8-10]. 近年來, 研究人員[11-15]提出了一種新穎的熱處理工藝: 淬火(quenching)+C配分(partitioning). 其具體工藝流程為: 首先把材料加熱到奧氏體化溫度, 然后淬火到馬氏體轉(zhuǎn)變開始溫度和終了溫度之間的某一溫度, 再在該淬火溫度(或者淬火溫度以上的某一溫度停留一段時間, 稱為Q&P兩步法處理[16,17])下保溫一定時間使C由馬氏體向殘余奧氏體配分, 此時馬氏體中的C含量下降, 奧氏體中的C含量升高, 使殘余奧氏體富C提高其熱穩(wěn)定性從而能夠?qū)⒉糠謯W氏體穩(wěn)定至室溫, 最后獲得馬氏體與殘余奧氏體復(fù)合組織.
當(dāng)前在Q&P鋼的生產(chǎn)中, 為保證獲得超高強(qiáng)度以及較多的殘余奧氏體, 采取的是提高鋼中C的添加量的方法, 一般C含量都要在0.3%~0.5% (質(zhì)量分?jǐn)?shù))[18,19]. 但是鋼中C含量增加會使冷卻過程中由奧氏體轉(zhuǎn)變的馬氏體中出現(xiàn)大量孿晶, 硬度提高, 塑性和韌性降低; 過高的含C量會造成過多的碳化物形成, 降低C在奧氏體中的固溶量, 從而誘發(fā)殘余奧氏體的分解, 并且對C配分過程造成干擾, 這也是導(dǎo)致塑性偏低的一個重要原因. 同時, 高的C含量也會加大鋼的淬透性, 在焊接時增大熱影響區(qū)容易發(fā)生焊接開裂, 降低焊接性能[20,21], 致使性能指標(biāo)不能滿足汽車用鋼要求. 而為保證Q&P鋼具備良好的焊接性能, 需使得鋼中C含量控制在較低水平, 這將導(dǎo)致室溫下殘余奧氏體的組織穩(wěn)定性和機(jī)械穩(wěn)定性受到較大影響[22]. 因此, 為保證高強(qiáng)鋼的力學(xué)性能與焊接性能之間平衡, 尋求利用其它合金元素配分提高殘余奧氏體穩(wěn)定性、探索與其相對應(yīng)的高強(qiáng)鋼制備工藝及參數(shù)等已成為亟待解決的科學(xué)問題. 上世紀(jì)80年代初, 研究人員[23]在對鋼進(jìn)行奧氏體化處理時發(fā)現(xiàn), Cr和Mn等奧氏體穩(wěn)定元素通過擴(kuò)散作用可以減緩隨后冷卻過程中的奧氏體相變, 但其并沒有將此特殊現(xiàn)象用于改進(jìn)鋼的組織性能. Lee等[24,25]在對超細(xì)晶的TRIP鋼進(jìn)行臨界區(qū)退火時發(fā)現(xiàn), Mn元素在奧氏體與馬氏體兩相中的平衡濃度發(fā)生變化, Mn元素明顯在奧氏體相中出現(xiàn)富集, 對提高奧氏體的穩(wěn)定性起到一定作用. 然而, 目前對于Mn元素在高強(qiáng)鋼中的配分機(jī)制以及對室溫殘余奧氏體機(jī)械穩(wěn)定性的影響尚未進(jìn)行過較為系統(tǒng)的研究.
因此, 本工作以C-Si-Mn系高強(qiáng)鋼為研究對象, 圍繞提高殘余奧氏體含量及其機(jī)械穩(wěn)定性等關(guān)鍵問題, 開展合金元素配分工藝及微觀組織控制的研究. 采用在雙相區(qū)保溫+奧氏體化淬火+低溫退火的熱處理工藝, 就Mn元素雙相區(qū)配分行為對組織演變及力學(xué)性能的影響進(jìn)行了表征. 對探索合金元素配分的理論和機(jī)制有重要意義, 為當(dāng)前開發(fā)適用于汽車輕量化發(fā)展需求的先進(jìn)高強(qiáng)鋼提供實踐基礎(chǔ).
1 實驗方法
實驗用鋼采用50 kg真空熔煉爐冶煉, 其化學(xué)成分(質(zhì)量分?jǐn)?shù), %)為: C 0.20, Si 0.37, Mn 1.28, P 0.0032, S 0.0014, B 0.0018, 余量為Fe. 實驗鋼的Ac3=844 ℃, Ac1=718 ℃, Ms=345 ℃(Ac3為加熱時先共析鐵素體全部轉(zhuǎn)變成奧氏體的終了溫度, Ac1為加熱時珠光體向奧氏體轉(zhuǎn)變的開始溫度, Ms為冷卻時馬氏體初始轉(zhuǎn)變溫度). 將冶煉后鋼錠鍛造并剪切成50 mm×50 mm×100 mm方坯, 在二輥熱軋實驗機(jī)上軋制得到厚度為3.5 mm的熱軋板坯, 經(jīng)5道次冷軋得到厚度為1.5 mm鋼板.
圖1a為雙相區(qū)保溫后直接淬火(I&Q)的工藝流程圖, 采用雙相區(qū)760 ℃進(jìn)行保溫加熱, 保溫時間為600, 1000, 1300和1500 s, 使之生成一定比例的鐵素體和奧氏體, 通過保溫使Mn元素由鐵素體向奧氏體中進(jìn)行擴(kuò)散, 之后水淬到室溫, 通過觀測室溫下Mn元素在鐵素體和馬氏體兩相中的元素分布, 驗證雙相區(qū)的元素配分行為. 圖1b為傳統(tǒng)淬火+低溫退火(Q&P)處理工藝流程圖, 將實驗用鋼加熱到奧氏體化溫度(AT=930 ℃)并保溫120 s, 使之完全奧氏體化, 然后采用鹽浴淬火使其快速冷卻到Ms~Mf (Mf為冷卻時馬氏體轉(zhuǎn)變的終了溫度)之間的某一溫度(奧氏體化后冷卻時淬火溫度QT=220 ℃, 由馬氏體含量計算公式Krauss-Koistinen-Marburger公式[26,27]所得)并保溫15 s, 最終水淬至室溫. 圖1c為雙相區(qū)保溫+奧氏體化淬火+低溫退火(I&Q&P)工藝流程圖, 先將實驗用鋼加熱到雙相區(qū)760 ℃保溫1300 s, 之后快速加熱到奧氏體化溫度(AT=930 ℃)并保溫120 s, 然后淬火至QT=220 ℃保溫15 s, 最終水淬至室溫.
Fig.1 不同熱處理工藝流程圖
將試樣經(jīng)不同工藝處理, 經(jīng)過研磨、拋光和4%硝酸酒精(體積分?jǐn)?shù))浸濕后, 采用Axiovert200MAT光學(xué)顯微鏡(OM)和S-4800場發(fā)射掃描電鏡(SEM)進(jìn)行顯微組織觀察及分析; 采用線切割按照GB/T228-2002標(biāo)準(zhǔn)制取拉伸實驗樣品, 在WBW-600B液壓萬能試驗機(jī)上進(jìn)行拉伸實驗; 利用D/MAX2500PC X射線衍射儀(XRD)分析實驗用鋼中的殘余奧氏體, 實驗參數(shù)為: Cu靶, 步寬0.02°, 功率40 V, 電流150 mA, 實驗角度范圍60°~100°, 速度10 °/min, 測定精確的衍射角2θ和積分強(qiáng)度I, 按國標(biāo)GB8362-87對殘余奧氏體的體積分?jǐn)?shù)進(jìn)行分析, 利用奧氏體(220)γ, (200)γ, (311)γ和馬氏體(211)α′, (220)α′晶面的積分強(qiáng)度通過直接比較法[28]計算出殘余奧氏體含量. 利用裝配有Oxford-EBSD成像系統(tǒng)的JXA-8230型電子探針(EMPA), 觀察經(jīng)圖1a和圖1c工藝制備的試樣室溫下的微觀組織形貌以及Mn元素在兩相中的濃度分布情況, EMPA工作電壓為20 kV, 二次電子分辨率為5 nm.
2 實驗結(jié)果及分析
2.1 I&Q工藝Mn元素配分行為
圖2為雙相區(qū)760 ℃保溫并淬火后鋼的SEM像. 由圖可知, 試樣的原始組織為鐵素體(F)和珠光體(P)組織, 經(jīng)雙相區(qū)保溫并淬火后, 試樣的室溫組織主要由鐵素體(F)和板條馬氏體(M)組成, 隨著雙相區(qū)保溫時間的延長, 室溫馬氏體體積分?jǐn)?shù)逐漸增多, 當(dāng)保溫時間達(dá)到1000 s時, 室溫馬氏體體積分?jǐn)?shù)達(dá)到最大值55%, 如圖2d所示. 當(dāng)保溫時間進(jìn)一步延長時, 馬氏體和鐵素體兩相趨于平衡, 室溫馬氏體體積分?jǐn)?shù)隨不同保溫時間的變化曲線如圖3所示, 說明在雙相區(qū)進(jìn)行保溫時, 雙相區(qū)中奧氏體體積分?jǐn)?shù)會隨著保溫時間的延長逐漸增多直至達(dá)到飽和, 之后隨著保溫時間進(jìn)一步延長, 奧氏體和鐵素體兩相趨于平衡.
Fig.2 760 ℃保溫不同時間并淬火后鋼的SEM像
圖4和5為雙相區(qū)760 ℃保溫并直接淬火后鋼的EBSD像及Mn元素分布的EMPA像. 由圖可知, 在原始組織中(圖4a), Mn分布均勻, 鐵素體與珠光體中Mn含量基本相等, 當(dāng)加熱到760 ℃保溫300 s并淬火后, 室溫組織中出現(xiàn)少量馬氏體組織, Mn開始出現(xiàn)不均勻分布現(xiàn)象, 馬氏體中Mn含量稍高于鐵素體, 說明此時雙相區(qū)中Mn已經(jīng)發(fā)生了從鐵素體向奧氏體中的擴(kuò)散. 當(dāng)保溫時間達(dá)到600 s時, 試樣的室溫組織已呈現(xiàn)出典型的馬氏體和鐵素體兩相組織, 由EMPA像中能明顯看到馬氏體中的Mn含量高于鐵素體中的Mn含量. 隨著保溫時間的延長, 向奧氏體中擴(kuò)散的Mn含量逐漸增多, 當(dāng)保溫時間增至1300 s時, Mn在鐵素體與奧氏體兩相中化學(xué)勢達(dá)到平衡, 不再進(jìn)行兩相間的擴(kuò)散, 并且當(dāng)保溫時間為1300 s時雙相區(qū)奧氏體中Mn含量達(dá)到最大值2.51%, 而隨著時間的進(jìn)一步延長, 奧氏體和鐵素體兩相雖趨于平衡, 但雙相區(qū)組織仍呈現(xiàn)長大趨勢, 使得Mn在奧氏體中含量相對減少, 鋼中馬氏體的Mn含量變化趨勢如圖6所示.
Fig.3 不同保溫時間對馬氏體體積分?jǐn)?shù)的影響
2.2 Q&P和I&Q&P工藝處理后鋼的微觀組織
圖7為經(jīng)不同工藝處理后鋼的SEM像. 由圖7a可知, 經(jīng)Q&P工藝處理后, 室溫組織主要由少量板條狀馬氏體、少量板條間彌散分布的碳化物顆粒和極少量的殘余奧氏體組成, 還存在較多的塊狀組織, 這是經(jīng)最終淬火時未轉(zhuǎn)變奧氏體發(fā)生馬氏體轉(zhuǎn)變, 形成的二次淬火馬氏體(M2)或殘余奧氏體(RA), 呈規(guī)則幾何形狀, 無明顯析出物. 在傳統(tǒng)Q&P工藝奧氏體化鹽浴淬火過程中, 將得到一定量的板條狀一次淬火馬氏體(M1), 此時C元素由一次淬火馬氏體向未轉(zhuǎn)變的奧氏體擴(kuò)散使之趨于穩(wěn)定, 由于鹽浴淬火冷卻速度較低, 配分過程中一次淬火馬氏體會發(fā)生自回火分解, 馬氏體板條邊界較模糊, 產(chǎn)生顆粒狀白色碳化物析出, 而較低的Si含量對碳化物抑制作用較小, 致使最終室溫下鋼的延展性能變差; 之后經(jīng)水淬至室溫時, 由于冷速較快且C配分對奧氏體的穩(wěn)定性影響較小, 一部分未轉(zhuǎn)變的奧氏體發(fā)生馬氏體轉(zhuǎn)變, 室溫組織中出現(xiàn)部分二次淬火馬氏體或殘余奧氏體. 由圖7b可知, 經(jīng)I&Q&P工藝處理后, 室溫組織主要由大量板條狀馬氏體、少量板條間彌散分布的碳化物顆粒和殘余奧氏體組成, 存在少量的塊狀組織. 經(jīng)雙相區(qū)加熱保溫時, 鐵素體中Mn元素隨著保溫時間的延長向奧氏體中逐漸擴(kuò)散直至達(dá)到化學(xué)勢平衡, 之后加熱至奧氏體化溫度, 此時由鐵素體轉(zhuǎn)變成的奧氏體組織中Mn元素的含量大大降低, 再經(jīng)鹽浴淬火時, 此部分奧氏體全部轉(zhuǎn)變?yōu)橐淮未慊瘃R氏體, 而未轉(zhuǎn)變的奧氏體由于其Mn元素含量較高, 能穩(wěn)定到室溫, 而之后經(jīng)水淬至室溫時, 只有少量Mn元素含量較少的未轉(zhuǎn)變奧氏體發(fā)生馬氏體轉(zhuǎn)變, 其余則保留至室溫, 而雙相區(qū)保溫時, 鐵素體中的C元素由于較高的自由能, 使得其在較短的時間已經(jīng)完成了向奧氏體的擴(kuò)散, 而QT階段得到的一次淬火馬氏體由于其C元素含量較低, 致使自回火產(chǎn)生的白色碳化物顆粒較少, 從而室溫組織中板條馬氏體量較多.
Fig.4 760 ℃保溫不同時間并淬火后鋼的EBSD像
圖8為經(jīng)I&Q&P處理后鋼的室溫組織中馬氏體和殘余奧氏體的Mn元素分布情況. 由圖可見, 實驗用鋼經(jīng)I&Q&P處理后通過EMPA能觀察到Mn元素在室溫組織的馬氏體和殘余奧氏體中較為明顯的不均勻分布情況, 薄膜狀殘余奧氏體在室溫中存在于馬氏體板條間. 從圖8中A和B位置可以看出, 位于馬氏體板條間的殘余奧氏體中Mn元素含量明顯高于馬氏體基體, 這是由于當(dāng)Mn元素在雙相區(qū)達(dá)到化學(xué)勢平衡時, 雙相區(qū)奧氏體中Mn元素含量達(dá)到最大值, 又經(jīng)淬火+低溫退火處理后, 這部分富Mn的奧氏體經(jīng)鹽浴淬火時可以穩(wěn)定下來, 該部分未轉(zhuǎn)變的奧氏體由于較高的Mn元素含量使得大部分能夠保留到室溫形成殘余奧氏體, 只有少量會發(fā)生馬氏體轉(zhuǎn)變. 可見, I&Q&P工藝對穩(wěn)定鋼中殘余奧氏體以及提高室溫殘余奧氏體含量起到了良好的作用, 而這種軟硬搭配的多相組織結(jié)構(gòu)也可為實驗鋼提供更高的強(qiáng)度和塑性.
Fig.5 760 ℃保溫不同時間并淬火后鋼中Mn元素分布的EMPA像
Fig.6 760 ℃保溫不同時間并淬火后鋼中馬氏體的Mn含量變化趨勢
2.3 Q&P和I&Q&P工藝處理后鋼中殘余奧氏體含量和力學(xué)性能
圖9為實驗鋼經(jīng)Q&P工藝和I&Q&P工藝處理后殘余奧氏體的XRD譜. 由圖可知, 直接經(jīng)Q&P處理的試樣中有2個奧氏體峰, 且峰值強(qiáng)度偏低, 而經(jīng)I&Q&P處理后的試樣的XRD譜中明顯觀測到在60°~100°間又出現(xiàn)了2個晶面的奧氏體衍射峰, 分別是(311)γ和(220)γ, 說明雙相區(qū)Mn元素的擴(kuò)散對奧氏體起到良好的穩(wěn)定作用, 從而使室溫下保留了更多的殘余奧氏體, 提高了鋼的塑性.
經(jīng)Q&P和I&Q&P工藝處理后鋼的力學(xué)性能見表1. 由表可知, 實驗鋼的原始力學(xué)性能中, 抗拉強(qiáng)度為640 MPa, 延伸率為26.0%, 其原始組織為鐵素體和珠光體組織. Q&P工藝處理后, 其抗拉強(qiáng)度為1560 MPa, 延伸率為8.3%, 強(qiáng)塑積為12948 MPa·%, 而經(jīng)I&Q&P處理后, 與Q&P工藝相比, 鋼的抗拉強(qiáng)度略有降低為1310 MPa, 延伸率有顯著提高為12.0%, 強(qiáng)塑積為15720 MPa·%, 強(qiáng)塑積比Q&P工藝下提高了約20%.
Fig.7 不同工藝處理后鋼的SEM像
Fig.8 I&Q&P處理后鋼中馬氏體和殘余奧氏體的Mn元素分布
3 I&Q&P工藝各階段組織演變分析討論
圖10為I&Q&P工藝各階段鋼的組織演變模型. γI為雙相區(qū)奧氏體,γA表示雙相區(qū)鐵素體在AT階段轉(zhuǎn)變而成的奧氏體, γ′表示為雙相區(qū)奧氏體在AT階段轉(zhuǎn)變而成的奧氏體, γ″表示為穩(wěn)定到室溫的殘余奧氏體, M1表示為鹽浴淬火階段先形成的一次淬火馬氏體, M2表示為最終水淬階段形成的二次淬火馬氏體. 由圖可知, 實驗用鋼經(jīng)冷軋后室溫組織主要為鐵素體和珠光體, 其中各相Mn元素含量相同. 加熱到雙相區(qū)進(jìn)行保溫時, 珠光體首先轉(zhuǎn)變?yōu)閵W氏體γI, 隨著保溫時間的延長, 雙相區(qū)奧氏體逐漸增多直至達(dá)到兩相平衡, 而鐵素體中Mn元素也會伴隨時間的延長向奧氏體中發(fā)生擴(kuò)散, 直至達(dá)到化學(xué)勢平衡, 此時鋼的組織為鐵素體和奧氏體, 且奧氏體中Mn元素含量明顯高于鐵素體. 隨后升溫至奧氏體化(AT)進(jìn)行保溫時, 雙相區(qū)的鐵素體轉(zhuǎn)變?yōu)镸n元素含量較少的奧氏體γA, 而雙相區(qū)的奧氏體γI轉(zhuǎn)變?yōu)楦籑n的奧氏體γ′, 之后鹽浴淬火至QT階段時, 奧氏體γA由于其穩(wěn)定性元素Mn含量較少使得其在淬火時全部轉(zhuǎn)變?yōu)橐淮未慊瘃R氏體M1, 而富Mn的奧氏體γ′在此階段則大部分可以保留下來, 只有少量發(fā)生馬氏體轉(zhuǎn)變, 且未轉(zhuǎn)變的奧氏體γ′中Mn元素含量高于一次淬火馬氏體. 最后經(jīng)水淬至室溫的過程中, 奧氏體γ′由于較高M(jìn)n元素含量最終能夠穩(wěn)定到室溫, 得到殘余奧氏體γ″, 只有少量發(fā)生二次馬氏體轉(zhuǎn)變, 而殘余奧氏體γ″中Mn元素含量也明顯高于鋼中馬氏體的Mn元素含量.
Fig.9 不同工藝下鋼的XRD譜
表1 不同工藝處理后鋼的力學(xué)性能
圖10 I&Q&P工藝各階段組織演變過程模型
值得指出的是, 經(jīng)Q&P工藝處理的試樣只含有少量由C配分作用穩(wěn)定的殘余奧氏體, 而I&Q&P工藝處理后的試樣其室溫殘余奧氏體由富Mn的殘余奧氏體和經(jīng)C配分作用穩(wěn)定的殘余奧氏體共同組成, 富Mn的殘余奧氏體其尺寸往往很小, 且Mn元素含量較高, 從而使高強(qiáng)鋼具備了更優(yōu)異的塑性.
4 結(jié)論
(1) 實驗用鋼經(jīng)雙相區(qū)保溫時, 隨著保溫時間延長, 奧氏體體積分?jǐn)?shù)逐漸增多, 保溫時間為1000 s時, 室溫馬氏體體積分?jǐn)?shù)達(dá)到最大值55%; 而鐵素體中向奧氏體擴(kuò)散的Mn元素含量也逐漸增多直至其在兩相間達(dá)到化學(xué)勢平衡, 并且當(dāng)保溫時間為1300 s時, 奧氏體中Mn元素含量達(dá)到最大值2.51%.
(2) 經(jīng)Q&P工藝處理后, 室溫組織為大量塊狀馬氏體、少量板條狀馬氏體、少量板條間彌散分布的碳化物顆粒和極少量的殘余奧氏體, 而經(jīng)I&Q&P工藝處理后, 室溫組織中塊狀馬氏體含量大幅減少, 主要為板條狀馬氏體形貌, 而殘余奧氏體含量顯著增多, 達(dá)到4.3%, 抗拉強(qiáng)度為1310 MPa, 延伸率為12.0%, 強(qiáng)塑積達(dá)到15720 MPa·%以上.
(3) Q&P工藝處理后鋼中只含有少量由C配分作用穩(wěn)定的殘余奧氏體, 而I&Q&P工藝處理后鋼中殘余奧氏體由富Mn的殘余奧氏體和經(jīng)C配分作用穩(wěn)定的殘余奧氏體組成, 顯著提高室溫下鋼中殘余奧氏體的含量和機(jī)械穩(wěn)定性, 從而提高高強(qiáng)鋼的室溫成形能力.
參考文獻(xiàn)
[1] Hayami S, Furukawa T. Microalloying 75. New York: Union Carbide Corp, 1977: 311
[2] Raabe D, Ponge D, Dmitrieva O, Sander B. Scr Mater, 2009; 60: 1141
[3] Matsumura O, Sakuma Y, Takechi H. ISIJ Int, 1992; 32: 1014
[4] Matsumura O, Sakuma Y, Takechi H. ISIJ Int, 1987; 27: 570
[5] Sugimoto K, Misu M, Kobayashi M, Shirasawa H. ISIJ Int, 1993; 33: 775
[6] Bouaziz O, Guelton N. Mater Sci Eng, 2001; A319-321: 246
[7] Barnett M R. Mater Sci Eng, 2007; A464: 1
[8] Rizzo F, Martins A R, Speer J G. Mater Sci Forum, 2007; 539-543: 4476
[9] Andrade H L, Akben M G, Jonas J J. Metall Trans, 1983; 14A: 1967
[10] Hashimoto S, Ikeda S, Sugimoto K I, Miyake S. ISIJ Int, 2004; 44: 1590
[11] Speer J G, Matlock D K, De Cooman B C, Schroch J G. Acta Mater, 2003; 51: 2611
[12] Edmonds D V, Rizzo F C, De Cooman B C, Matlock D K, Speer J G. Mater Sci Eng, 2006; A438-440: 25
[13] De Cooman B C, Speer J G. In: Lee H C ed., The 3rd Int Conf on Advanced Structural Steels, Gyeongju: The Korean Institute of Metals and Materials, 2006: 798
[14] Speer J G, Rizzo F C, Matlock D K, Edmonds D V. Mater Res, 2005; 8: 417
[15] Matlock D K, Br?utigam V E, Speer J G. Mater Sci Forum, 2003; 426: 1089
[16] Xu Z Y. Mater Sci Forum, 2007; 561-565: 2283
[17] Wang X D, Zhong N, Rong Y H, Xu Z Y. J Mater Res, 2009; 24: 261
[18] Zhong N. PhD Dissertation, Shanghai Jiao Tong University, 2009
[18] (鐘 寧. 上海交通大學(xué)博士學(xué)位論文, 2009)
[19] De Moor E, Lacroix S, Clarke A J, Penning J, Speer J G. Metall Mater Trans, 2008, 39A: 2586
[20] Dong X C, Zhang X, Chen Y Q. Iron Steel Vanadium Titanium, 2011; 32: 62
[20] (董現(xiàn)春, 張 熹, 陳延清. 鋼鐵釩鈦, 2011, 32: 62)
[21] Zhu B K, Li S B, Zhou H, Yang P. Welding Joining, 2007; (4): 40
[21] (朱丙坤, 李少兵, 周 浩, 楊 澍. 焊接, 2007; (4): 40)
[22] Saleh M H, Prietner R. Mater Proc Technol, 2001; 113: 587
[23] Toji Y, Yamashita T, Nakajima K, Okuda K, Matsuda H, Hasegawa K, Seto K. ISIJ Int, 2011; 51: 818
[24] Lee S, Lee S J, De Cooman B C. Sci Mater, 2011; 65: 225
[25] Lee S J, Lee S, De Cooman B C. Sci Mater, 2011; 64: 649
[26] Krauss G. In: Rohatgi P K, Yust C S eds., Tribology of Composite Materials, Materials Park, Ohio: ASM International, 1990: 56
[27] Koistinen D P, Marburger R E. Acta Metall, 1959; 7: 59
[28] Fan X. Metallic X-ray Physics. Beijing: Mechanical Industry Press, 1989: 159
[28] (范 雄. 金屬X射線學(xué). 北京: 機(jī)械工業(yè)出版社, 1989: 159)
免責(zé)聲明:本網(wǎng)站所轉(zhuǎn)載的文字、圖片與視頻資料版權(quán)歸原創(chuàng)作者所有,如果涉及侵權(quán),請第一時間聯(lián)系本網(wǎng)刪除。
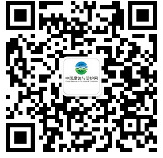
官方微信
《腐蝕與防護(hù)網(wǎng)電子期刊》征訂啟事
- 投稿聯(lián)系:編輯部
- 電話:010-62316606
- 郵箱:fsfhzy666@163.com
- 腐蝕與防護(hù)網(wǎng)官方QQ群:140808414