全球塑料年需求量預計2050年將超11億噸,但其生產嚴重依賴化石資源,2020年全生命周期溫室氣體排放達24.5億噸CO?當量。5-羥甲基糠醛(HMF)電氧化制備2,5-呋喃二甲酸(FDCA)是合成可再生聚酯的關鍵路徑,但傳統熱催化需高溫高壓及貴金屬催化劑,且存在副反應問題。此前千瓦級電流密度下的高選擇性FDCA電合成始終未能突破,主要受限于電極界面傳質不足、非法拉第副反應(如HMF縮合生成腐殖質)以及分子滲透等問題。
北京化工大學邵明飛、周華和清華大學段昊泓開發出一種固體聚合物電解質(SPE)反應器,通過工程化設計成功實現HMF的高選擇性電氧化。該反應器在1.5 A cm?²工業級電流密度下,以97.0%選擇性和88.2%法拉第效率穩定生產高濃度FDCA(~1.24 M),連續運行140小時性能無衰減。進一步構建的4.3 kW模塊化電化學平臺,達到33公斤/日的FDCA中試規模產能,較先前技術提升1-2個數量級。
反應器創新設計
團隊提出系統性解決方案:1)采用催化劑涂層膜(CCM)集成陽極(NiCoMoO?)和陰極(RuO?),消除陰極液以抑制分子滲透,使HMF/FDCA跨膜通量降低10倍;2)優化多孔傳輸層(PTL)結構,組合菱形網格/泡沫鎳/鎳網(RSG/NF/NM)形成湍流,增強徑向對流傳質;3)蛇形流場設計使電解液流速提升10倍(28.8 cm s?¹);4)陽極板集成冷卻腔控制溫度<30°C,抑制HMF高溫縮合副反應。200 cm²單模塊測試表明(圖2h),在0.5 A cm?²電流密度下連續運行140小時,FDCA產率保持88.1 g h?¹,濃度達1.27 M。
圖1 | HMF電氧化制備FDCA的背景、演示與挑戰。
圖2 | SPE反應器設計與性能。
關鍵組件優化
對比實驗驗證了組件必要性:采用PTL-2(含RSG)與蛇形流場時,FDCA法拉第效率達84.5%,較基礎PTL-1提升32%。流體模擬顯示RSG結構產生大渦流,顯著增強電極表面徑向傳質。冷卻系統則使反應溫度控制在29°C,避免82°C高溫導致的FDCA選擇性驟降至40.9%,并抑制腐殖質生成,將副反應導向可轉化的Cannizzaro產物。
圖3 | SPE關鍵組件優化對HMFOR的影響。
運行參數調控
高濃度HMF(1.4 M)將OER競爭反應壓制至10.3%法拉第效率,使FDCA產率在1.5 A cm?²下提升至654 W功率。無陰極液設計將FDCA濃度提升至1.34 M(歷史最高),同時單程模式將HMF停留時間縮至2.9分鐘,較循環模式提升選擇性20%。能耗降至2.54 kWh/kg FDCA,低于文獻報道值。
圖4 | 運行條件對HMFOR的影響。
中試應用展示
八臺SPE反應器并聯的4.3 kW平臺(圖5a)在1.0 A cm?²電流密度下,以88.7%法拉第效率日產FDCA 33公斤,同步產生高純氫氣(0.67 m³ h?¹)。所得FDCA成功用于生物基塑料制造:與乙二醇聚合生成聚呋喃二甲酸乙二醇酯(PEF)熱塑性塑料,經3D打印成定制結構(圖5e);與木質素衍生胺單體結合形成可回收環氧樹脂,模壓為"THU/BUCT"字母標識(圖5f)。經濟分析表明,通過聯產K?SO?和H?,FDCA成本可降至1301美元/噸,媲美熱化學工藝。
圖5 | 千瓦級FDCA生產與生物塑料應用
工業前景展望
該工作首次實現千瓦級生物質單體的高選擇性電合成,為可持續塑料產業提供了可放大的技術原型。未來需開發更大電極面積的反應器、優化電解質循環系統,并降低HMF原料成本。研究團隊強調,電化學路徑有望推動塑料工業從"石油基線性模式"向"生物質閉環模式"轉型,助力碳中和目標實現。
免責聲明:本網站所轉載的文字、圖片與視頻資料版權歸原創作者所有,如果涉及侵權,請第一時間聯系本網刪除。
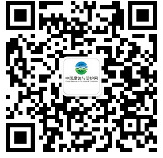
官方微信
《腐蝕與防護網電子期刊》征訂啟事
- 投稿聯系:編輯部
- 電話:010-62316606
- 郵箱:fsfhzy666@163.com
- 腐蝕與防護網官方QQ群:140808414