增材制造(AM)為先進裝備復雜高性能金屬部件加工帶來了巨大潛力。然而,在成型中不可避免會遺留熔池軌跡和微觀缺陷。作為增材金屬的本質物理印記,深入理解這些微結構如何影響材料的力學性能和服役行為,已成為其走向重大工程裝備的關鍵問題。近日,西南交通大學、澳大利亞新南威爾士大學、中國科學院高能物理研究所、四川大學、英國曼徹斯特大學等5家單位聯合,綜合應用原位高時空分辨同步輻射X射線微/納米三維成像及X射線衍射技術,首次原位追蹤到不同載荷下增材鋁合金內部損傷行為,揭示了熔池微結構(MPB)和缺陷在試樣全壽命期內的演化過程和相互作用關系,闡明了不同加載條件下廣域分布的MPB微結構和缺陷在疲勞損傷與斷裂過程中的主導作用,并提出了從對MPB微結構不敏感到敏感的疲勞裂紋擴展過渡的新機制。基于這一發現,研究團隊進一步引入物理信息驅動的神經網絡(PINN)機器學習模型,開發了一種將三維缺陷特征與增材鋁合金疲勞性能相關聯的新方法。這一新結果為增材制造金屬在不同應用場景的結構優化設計和部件服役性能評價提供了新的實驗證據和理論參考,有望推動該技術在航空航天、軌道交通、國防等關鍵行業中的廣泛應用。
最近,該項研究成果以“Critical damage events of 3D printed AlSi10Mg alloy via in situ synchrotron X-ray tomography”為題發表在工程結構材料頂級期刊《Acta Materialia》上。西南交通大學博士研究生吳正凱為論文第一作者(現職為日本九州大學項目助理教授,日本JSPS外籍特別研究員),西南交通大學吳圣川研究員和英國曼徹斯特大學PJ Withers院士(現職為澳大利亞莫納什大學訪問教授)為共同通訊作者,西南交通大學康國政教授和胡雅楠副教授、四川大學王清遠教授、澳大利亞新南威爾士大學Jamie J. Kruzic教授和Xiaopeng Li副教授以及中科院物理所張星星研究員為共同作者。該研究得到國家自然科學基金(U2032121、12192212)和西南交大新型交叉學科培育基金聯合資助。
研究背景
增材制造正以前所未有的速度推動制造業的數字化和低碳化轉型,其應用前景在過去的十年間迅速拓展。當前,金屬增材制造,尤其是激光粉末床熔融(L-PBF)技術,在關鍵工程金屬合金的設計和加工方面取得了顯著突破,涵蓋了鋁、鈦、鎂合金、鋼鐵、鎳基超合金、高熵合金等。L-PBF通過高能激光束逐層熔化金屬粉末,其間伴隨復雜而劇烈的熔化與凝固過程,由此制備的部件中將不可避免地存在大量熔池軌跡(例如,10 mm3的L-PBF金屬立方體內大約包含約104條熔池軌跡)及微觀制造缺陷(全域分布,且尺寸形貌復雜)。這些熔池結構(MPB)和微觀缺陷成為L-PBF金屬的固有特征。除熔池內部的微觀結構(如晶粒和胞狀結構等)外,這些MPB結構和微缺陷在很大程度上決定著L-PBF部件的力學性能,尤其是其疲勞損傷斷裂性能。然而,由于MPB和缺陷的復雜性及其跨尺度特征,長期以來在不同加載條件下量化它們對損傷失效機制的影響面臨巨大挑戰。此外,過去十幾年的研究主要集中于控制熔池內部的多尺度微觀結構來提升材料拉伸性能,而針對MPB和缺陷在不同加載條件下對疲勞性能影響的系統性研究仍不深入,極大限制了L-PBF技術在關鍵工程合金材料中的廣泛應用。
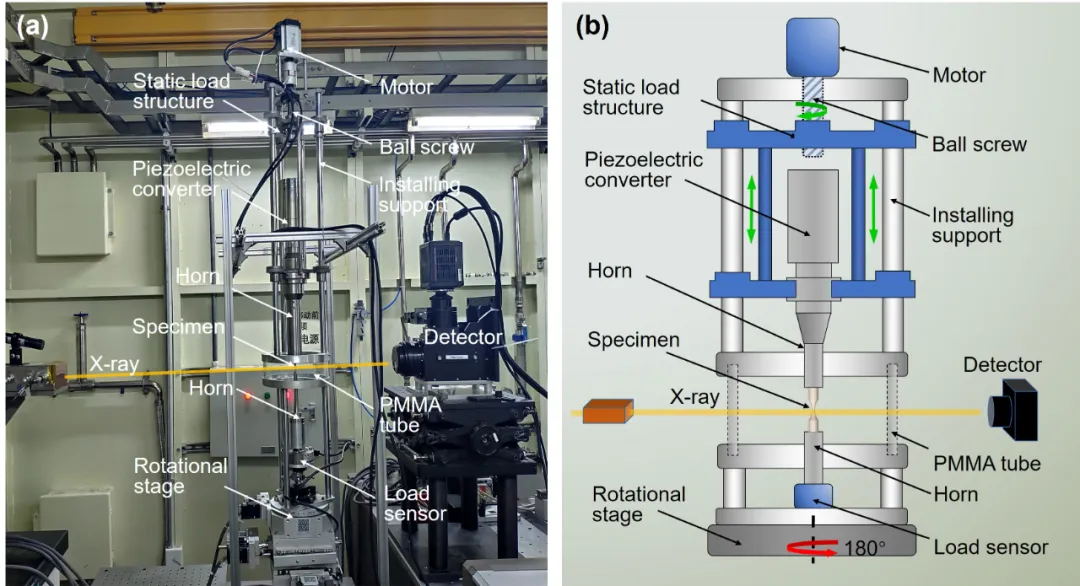
圖1 基于高分辨三維成像的增材制造鋁合金內部缺陷和MPB特征,以及微結構分布特征和相關力學性能
主要思路
本研究首先自主研制多功能(軸向拉伸、低周及高周疲勞)集成式原位三維成像加載裝置,結合高時空分辨率原位同步輻射X射線微米成像(Micro-CT)和X射線衍射(SXRD)技術,開展了不同加載模式下增材鋁合金內部微結構疲勞損傷與斷裂行為的高分辨三維定量表征,以探明不同載荷歷程下缺陷和MPB結構耦合機制。針對增材微結構與其力學性能的多尺度物理特征,綜合采用高空間分辨納米成像(Nano-CT)技術、EBSD和TEM等表征方法對臨界損傷區域進行多模態關聯表征,以闡明MPB損傷及微孔洞的形核模式,揭示不同加載模式下材料損傷破壞機制。最后,將三維缺陷特征對疲勞壽命的影響作為物理約束,進一步借助機器學習模型,建立三維缺陷特征與增材金屬疲勞性能的關系,從而實現對增材材料疲勞壽命的準確預測。
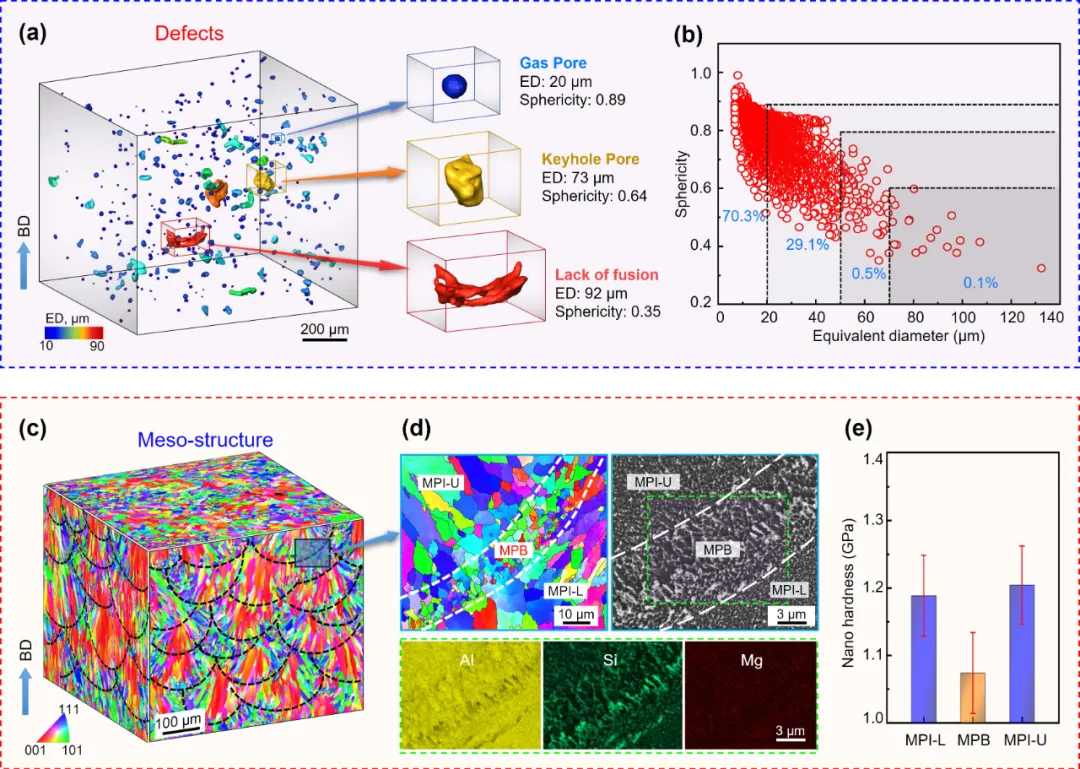
圖2 多功能集成原位加載系統及其原理圖
研究結果
本研究系統揭示了L-PBF制造成形的AlSi10Mg合金在拉伸、低周疲勞(LCF)和高周疲勞(HCF)加載條件下內部缺陷和損傷演化過程。結果發現,在高應變加載(拉伸、低周疲勞)下,與加載方向垂直的大尺寸缺陷導致微裂紋萌生和擴展,促進缺陷快速增長與連通。在此過程中,強度更低的MPB發生更大的塑性變形,MPB內粗大的硬質Si相與相對較軟的Al基體發生變形不匹配,促使MPB優先萌生微孔洞和裂紋,因此試樣內部裂紋橋接和擴展主要沿著MPB進行。而在低應力加載下(高周疲勞),疲勞壽命主要受裂紋源處的臨界缺陷主導,其余缺陷對疲勞性能的影響較小。另外,裂紋源缺陷的尺寸、取向、位置和形貌等特征對疲勞性能均具有顯著影響。

圖3 增材鋁合金在拉伸、LCF(σmax = 125% YS)和HCF(σmax = 60% YS)加載下內部缺陷演變與裂紋擴展行為,以及試樣三維CT成像(上圖)與局部放大(下圖)結果、試樣截面孔隙率變化曲線(右上)及相應的斷口損傷特征(右下圖)

圖4 (a) 微空洞主要成核于拉伸和LCF樣品的MPB中; (b) 試樣縱截面上幾何必須位錯(GNDs)分布;(c) TEM觀測和Si元素分布圖; (d) 通過原位SXRD測量的拉伸(左圖)加載下Al和Si相的應力變化以及 LCF加載期間的相應力變化(中間和右側)
在高應變條件下,內部損傷積累逐步加劇,微空洞首先在MPB處成核,裂紋隨后沿著MPB擴展;而在低應力加載條件下,表面缺陷主導了疲勞裂紋萌生過程,MPB的影響較為有限。在疲勞裂紋萌生和擴展過程中,隨著塑性區的增大,裂紋表現出從對MPB不敏感逐漸過渡到對MPB敏感并沿MPB開裂的擴展機制。研究結果為增材制造構件的疲勞性能評估與工藝優化提供了新思路,指出應根據不同工程應用需求制定缺陷控制與微結構調控策略,從而實現增材金屬材料的按需設計與安全評估。
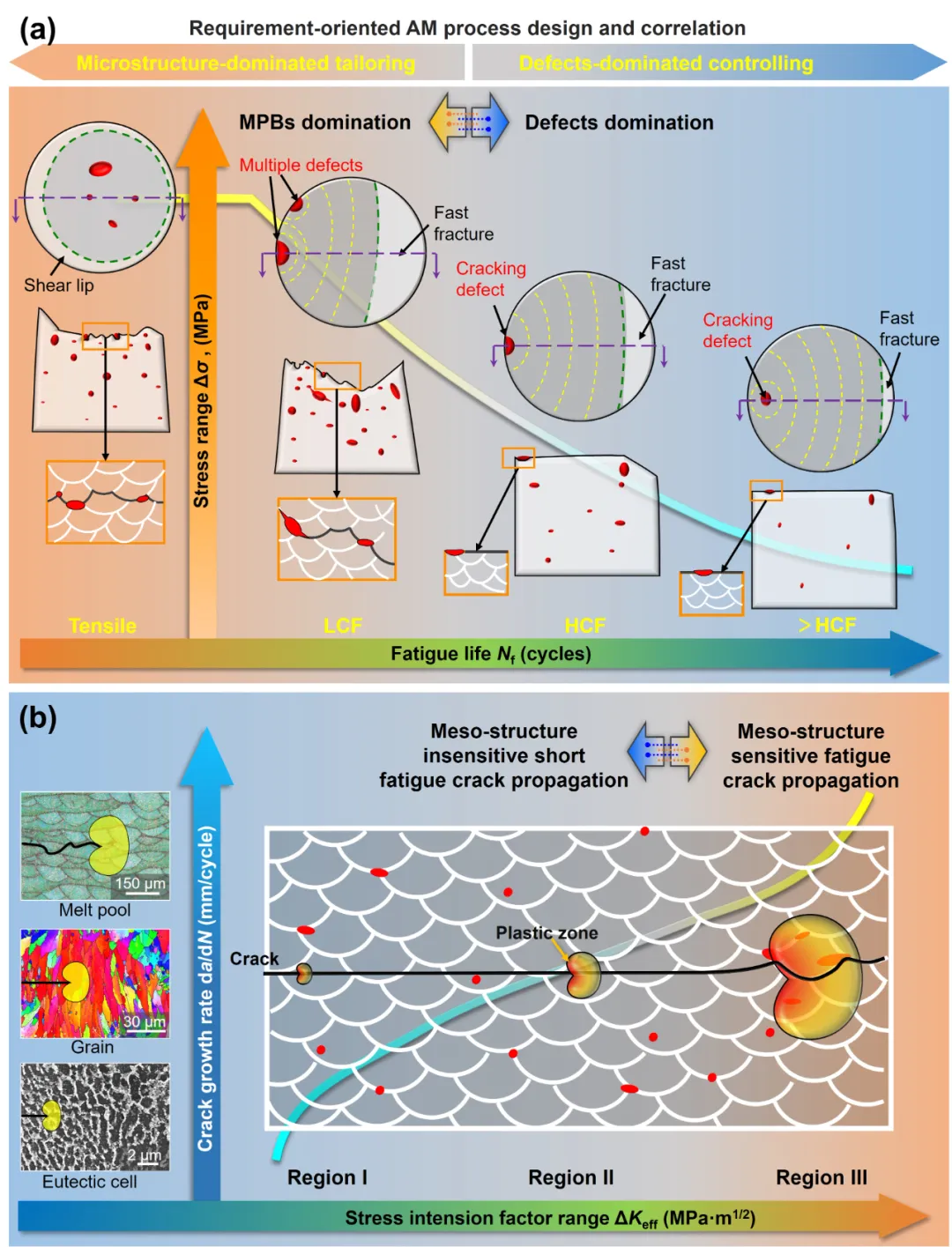
圖5 不同載荷歷程下增材合金的損傷失效行為: (a) 拉伸、LCF和 HCF加載條件下增材合金損傷失效機制示意圖;(b) 不同ΔKeff 水平下疲勞裂紋擴展行為的轉變,不同裂紋長度尺度的塑性區分別顯示出不同的疲勞裂紋-微結構相互作用機制
疲勞實驗發現,增材金屬部件的高周疲勞性能分散性顯著,且主要與主導裂紋萌生的關鍵缺陷的物理特征相關。通過X射線三維成像、疲勞測試和斷口分析,建立了關鍵缺陷三維特征與疲勞壽命的關聯數據集,進一步開發了引入物理約束的神經網絡模型(PINN),將缺陷幾何特征對疲勞壽命的影響納入損失函數,建立了一種將三維缺陷特征與疲勞性能相關聯的新方法,實現了增材金屬疲勞壽命的準確預測。
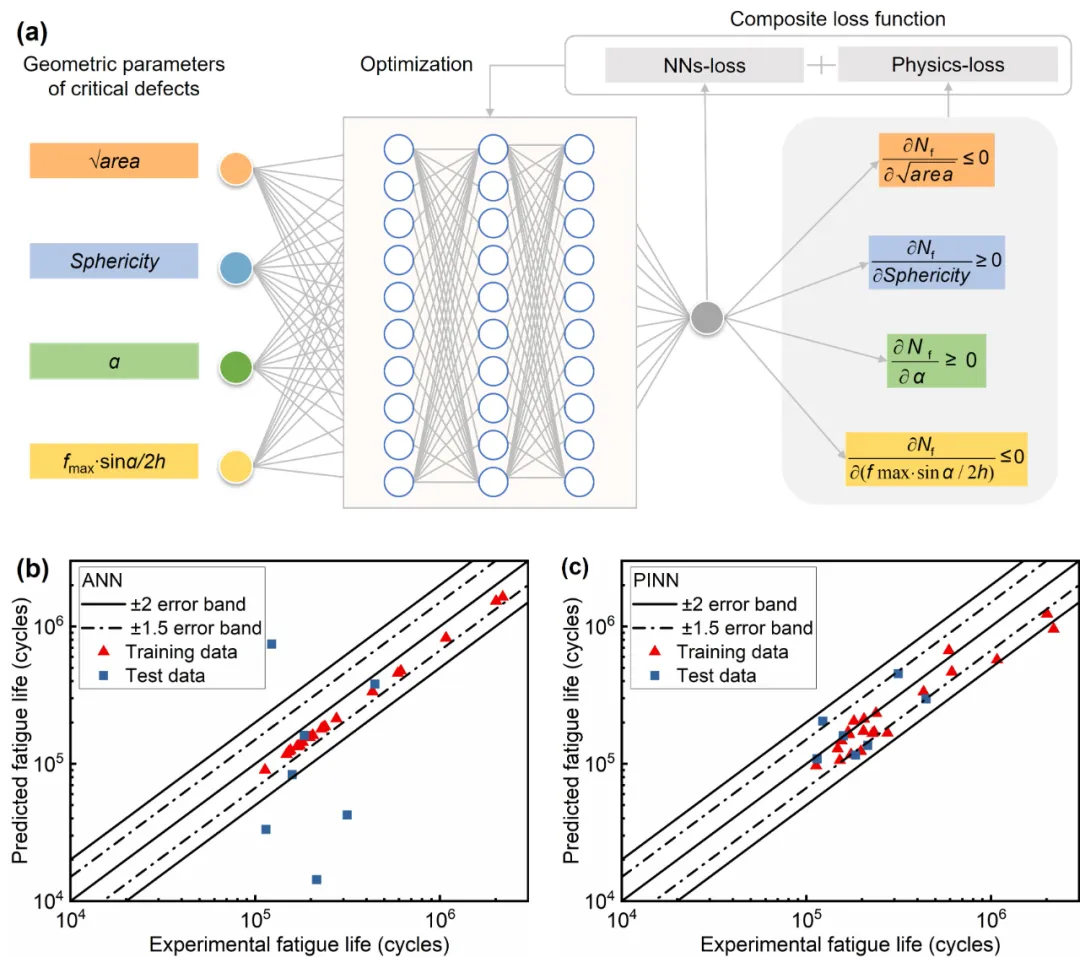
圖6 基于機器學習的疲勞壽命預測:(a) 基于關鍵缺陷幾何參數的 PINN 示意圖;基于 (b) ANN 和 (c) PINN 模型的疲勞壽命預測與實驗結果比較
總結與討論
增材制造應用場景日益廣泛,從功能件到關重件,從低周疲勞、高周疲勞到超高周疲勞材料部件,都具有巨大應用發展潛力,在航空航天、軌道交通、醫學、國防、能源等重要行業領域被“寄予厚望”,相關理論研究、資金投入、設備研發等也與日俱增。然而,由于增材制造本身涉及參數繁多、成型機理復雜、應用場景不一、評價標準欠缺,其工程應用仍存在較大技術障礙。目前,增材制備“完美無暇”材料成為學術界和工業界的共同追求目標,研究主要集中于去除缺陷、調控組織、降低殘余應力和表面粗糙度等,進而得到一種高強度、高塑形性且疲勞性能優異的構件,在此方面也取得了一定進展。但是,這種“高標準、嚴要求”并不總被接受,因為它會極大地提高研發和制造成本。眾所周知,焊接作為主要的成型工藝之一,在工業制造中同樣面對著焊接氣孔、組織不均勻、殘余應力等問題,但百余年來,其已廣泛應用于各關鍵工業領域,并發揮著無可替代的作用。因此,一般認為,增材制造技術作為一種先進制造工藝,在保持對其前沿課題研究的同時,應盡可能發揮其現有技術特色。例如,不同的應用場景對材料的服役性能要求截然不同,在工業應用中,“沒有問題”不可能,“問題可控”便可行。本研究正是基于此思想,綜合采用原位高分辨三維成像和跨尺度關聯表征系統研究了L-PBF增材AlSi10Mg合金在拉伸、低周疲勞和高周疲勞下的內部損傷演化過程和裂紋擴展機制,明確了高塑性加載下熔池微結構占主導,低應力加載下孔隙缺陷占主導的損傷斷裂模式,并提出了從對熔池結構敏感到不敏感的裂紋擴展過渡的新機制,這為不同應用場景下的增材材料工藝調控與設計明確了方向:以熔池微結構調控為主以提高其強韌性,以缺陷水平控制為主以提高其疲勞壽命,從而實現面向工程應用的增材制造部件定制化設計。此外,關鍵缺陷與疲勞壽命(尤其是高周、超高周疲勞)密切相關,“缺陷可控”通常比“消除缺陷”更具可行性,X射線三維成像在缺陷的空間幾何表征方面優勢顯著,隨著機器學習(ML),尤其是物理信息驅動的神經網絡模型(PINN)的發展,直接建立缺陷特征與疲勞性能的關系成為一種新的思路。這里需要指出的是,缺陷應不僅僅局限于通常意義上的定義,比如微觀組織異性和表面粗糙度也亦應被視為缺陷。不僅如此,機器學習在處理復雜多物理場信息方面優勢顯著,有望建立“工藝參數-微觀組織-缺陷特征-力學性能”(PSP)的定量化關系,從而促進增材制造技術的快速發展和應用,是未來增材制造材料開發、應用及性能評價過程中不可或缺的技術手段之一。
【通訊作者:吳圣川研究員wusc@swjtu.edu.cn(西南交通大學);Philip J. Withers院士p.j.withers@manchester.ac.uk(英國曼徹斯特大學)】
團隊簡介
近年來,西南交通大學吳圣川課題組研制了基于同步輻射光源三維成像技術的原位拉壓、微動疲勞、接觸磨損、軸向/旋彎疲勞及超高溫/超低溫/強腐蝕等先進材料結構內部損傷表征的系列原創裝置,提出了增材制造和焊接構件內部損傷的圖像力學方法(3D+時間+損傷),建立了應力水平-缺陷臨界-疲勞壽命的三參數K-T評定圖(或W-W參數模型),創立了基于先進光源的結構內部損傷原位跨尺度表征方向,入選《中國力學2035發展戰略》,基于高時空分辨的原位超高周疲勞試驗技術被國家標準《超高周疲勞超聲疲勞試驗方法》確定為第三方驗證方法,相關成果在Nature子刊、Acta Mater、Int J Mech Sci、Int J Fatigue等期刊發表,多篇入選ESI高被引論文,授權發明16件,出版論著《材料疲勞損傷行為的先進光源表征技術》和《增材制造先進材料及結構完整性》,試驗數據與模型被國際科研領軍軟件Thermo Fisher Scientific采納,兼任Int J Fatigue編委及Tomo Mater Struct創刊編委,部分成果支撐了2022年中國質量技術一等獎(排名2)。
相關參考文獻:
[1]Wu ZK, Wu SC, Qian WJ, Zhang HO, Zhu H, Chen QY, et al. Structural integrity issues of additively manufactured railway components: Progress and challenges. Eng Fail Anal 2023;149:107265. https://doi.org/10.1016/j.engfailanal.2023.107265.(綜述,ESI高被引)[2]Peng X, Wu SC, Qian WJ, Bao JG, Hu YN, Huang ZX, et al. The potency of defects on fatigue of additively manufactured metals. Int J Mech Sci 2022;221:107185. https://doi.org/10.1016/j.ijmecsci.2022.107185.(ESI高被引)[3]Qian WJ, Wu SC, Wu ZK, Ahmed S, Zhang W, Qian GA, et al. In situ X-ray imaging of fatigue crack growth from multiple defects in additively manufactured AlSi10Mg alloy. Int J Fatigue 2022;155:106616. https://doi.org/10.1016/j.ijfatigue.2021.106616.(ESI高被引)[4]Wu ZK, Wu SC, Bao JG, Qian WJ, Karabal S, Sun W, et al. The effect of defect population on the anisotropic fatigue resistance of AlSi10Mg alloy fabricated by laser powder bed fusion. Int J Fatigue 2021; 151: 106317. https://doi.org/10.1016/j.ijfatigue.2021.106317.(ESI高被引)[5]Bao HY, Wu SC, Wu ZK, Kang GZ, Peng X, Withers PJ. A machine-learning fatigue life prediction approach of additively manufactured metals. Eng Fract Mech 2021;242:107508. https://doi.org/10.1016/j.engfracmech.2020.107508.(ESI高被引)[6]Hu YN, Wu SC, Withers PJ, Zhang J, Bao HYX, Fu YN, et al. The effect of manufacturing defects on the fatigue life of selective laser melted Ti-6Al-4V structures. Mater Des 2020;192:108708. https://doi.org/10.1016/j.matdes.2020.108708.(ESI高被引)[7]Hu YN, Wu SC, Wu ZK, Zhong XL, Ahmed S, Karabal S, et al. A new approach to correlate the defect population with the fatigue life of selective laser melted Ti-6Al-4V alloy. Int J Fatigue 2020;136:105584. https://doi.org/10.1016/j.ijfatigue.2020.105584.(ESI高被引)[8]Zhang H, Li RS, Liu JJ, Wang KY, Qian WJ, Shi L, et al. State-of-art review on the process-structure-properties-performance linkage in wire arc additive manufacturing. Virtual Phys Prototyp 2024;19:e2390495. https://doi.org/10.1080/17452759.2024.2390495.(邀請綜述)[9]Hu YN, She YF, Wu SC, Kan QH, Yu H, Kang GZ. Critical physics informed fatigue life prediction of laser 3D printed AlSi10Mg alloys with mass internal defects. Int J Mech Sci 2024:109730. https://doi.org/10.1016/j.ijmecsci.2024.109730.[10]Wu ZK, Wu SC, Duan YS, Huang K, He WT, Du DF, et al. In situ X-ray tomography of fracture behaviour in low-porosity L-PBF AlSi10Mg alloy with laser shock peening. Virtual Phys Prototyp 2023;18:e2273955. https://doi.org/10.1080/17452759.2023.2273955.[11]Wu ZK, He ZA, Wu SC, Gao X, Lei L, Liu CK, et al. Rotating bending fatigue mechanisms of L-PBF manufactured Ti-6Al-4V alloys using in situ X-ray tomography. Int J Fatigue 2023;176:107876. https://doi.org/10.1016/j.ijfatigue.2023.107876.
[12]Wu ZK, Wu SC, Gao X, Lin Y, Xue YL, Withers PJ. The role of internal defects on anisotropic tensile failure of L-PBF AlSi10Mg alloys. Sci Rep 2023;13:14681. https://doi.org/10.1038/s41598-023-39948-z.